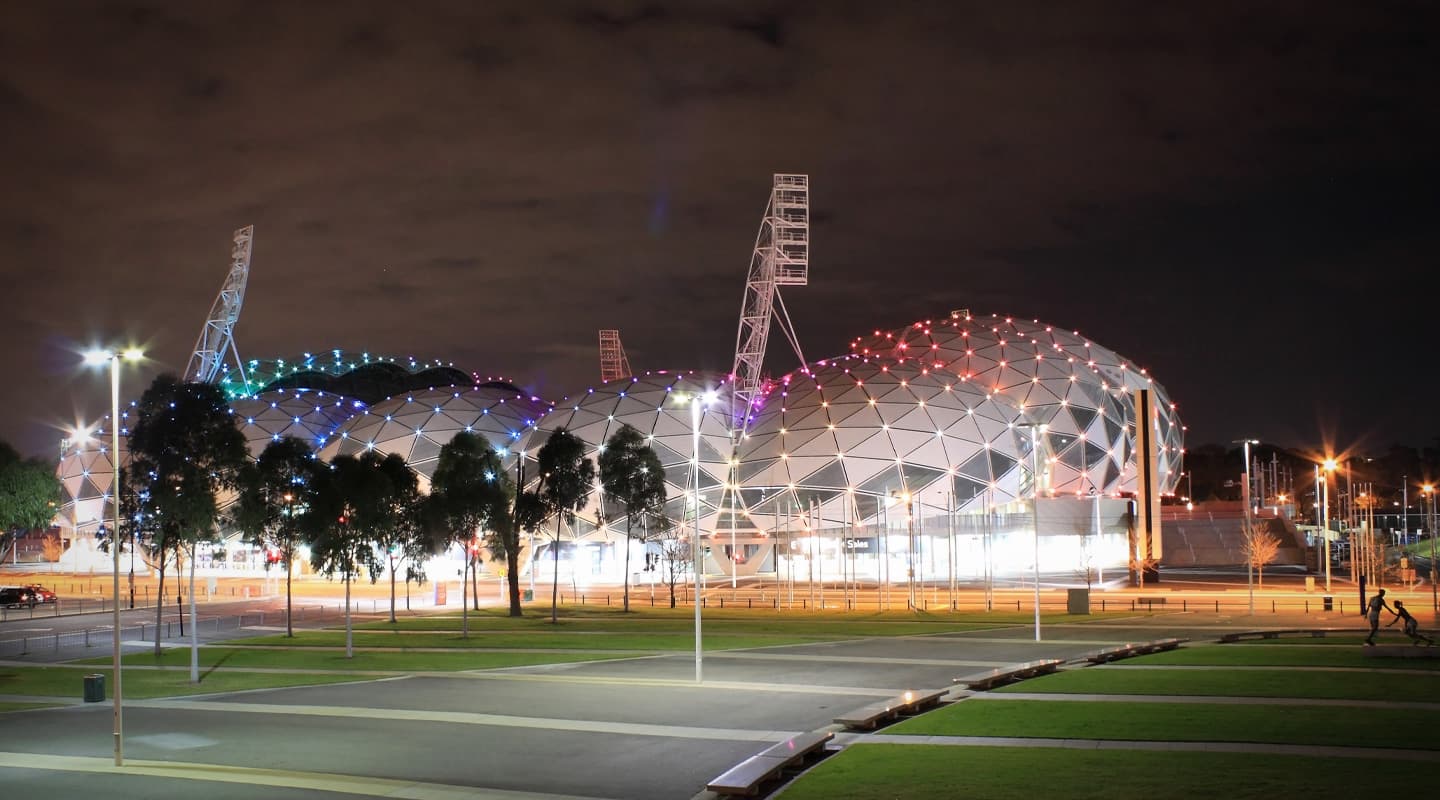
In The Right Ball Park
The AAMI Park install is a rectangular peg in a rectangular hole.
Text:/ Mandy Jones & Christopher Holder
In a city where sport is king, the completion of a new stadium is a big deal. Melbourne has long been well-equipped for cricket, AFL and tennis, but rugby and ‘the world game’ soccer have been noticeably lacking in world-class facilities. So when the Victorian State Government unveiled plans for a new rectangular stadium to be constructed on the Edwin Flack oval in Richmond, rugby and soccer players and fans alike hoped the result would be worth the wait.
After two and a half years of construction, the $267.5m stadium (now known as AAMI Park) is fully operational. Located in the heart of Melbourne’s sporting precinct next to Olympic Park and a stone’s throw from Rod Laver Arena and the mighty MCG, the impressive 30,050-seat rectangular stadium is purpose-built for soccer and both rugby codes, and the occasional concert.
The stadium is home to NRL team Melbourne Storm, A-League soccer teams Melbourne Victory and Melbourne Heart, and Super 15s rugby team Melbourne Rebels, all of whom have the benefit of fully equipped training facilities as well as a gymnasium, pool and change rooms. Other tenants in the stadium include the Victorian Olympic Council, Tennis Victoria, Melbourne Football Club and the Olympic Park Sports Medicine Centre. On game days, spectators have access to 14 public bars and retail food outlets, and a street level café is open everyday to service the stadium’s tenants and the general public. Corporate facilities include 24 corporate boxes with enviable views to the sunken pitch below and a large function room suitable for events up to 1000 guests.
Even though the stadium holds more than 30,000 spectators, as a space it has a remarkably intimate feel. Being rectangular in shape, spectators are so much closer to the action than when these sports are played on oval grounds.
Designed by Cox Architects and constructed by Grocon, the distinctive open-roof stadium has been a welcome addition to Melbourne’s expanding skyline. Comprised of large white shells, the stadium’s roof provides shelter for spectators while allowing direct sunlight onto the combination of natural turf on the playing surface itself and synthetic StaLok turf on the sidelines, ensuring a high quality playing surface. From a distance, the shells look like a fluffy white cloud, but upon closer inspection the interconnected triangle panels become apparent, and it is these triangular panels that are the key to the design. The triangles combine to form a lightweight steel bioframe of geodesic domes which provide incredible strength and structural integrity for the roof while using 50% less steel than a typical cantilever roof. Some 80% of the 20,000sqm of cladding on the roof is made of metal panels and the remaining 20% is glass panels, enabling even more natural light into the stadium and onto the pitch. While the clever design of the bioframe has obvious cost and sustainability benefits in its reduced use of steel, the benefit to supporters is in the un-interrupted sightlines to the pitch without columns or roof supports in their field of vision.
LIVE ON SCREENS
Stadiums are big audiovisual undertakings – that much is obvious. Rutledge Engineering know all about ‘big’ and if there’s an AV lesson to be learnt from AAMI Park, it’s that big doesn’t have to be over-awing or overly complex.
For Rutledge the project could be broken down into these main categories: the bowl PA, the MATV backbone, the comms, the facility-wide PA system and the screens. Each of those areas are big undertakings but they don’t have to be enormously complicated.
The most obvious AV is the sheer number of screens: screens in the concourse, screens in the corporate boxes, screens in the tuck shops, screens in the function rooms… screens galore. The Melbourne & Olympic Parks Trust (MOPT) has an obvious connection with Chinese electrical manufacturer Hisense (the Hisense Arena over the road is under MOPT’s management) and clearly the instruction has been to back up the Great Wall trucks and unload containers of 42-inch commercial panels.
Each screen is individually addressable – each is a LAN node – and can display free-to-air, live feeds from Foxtel, or presentations in the function rooms. Rutledge designed and built a custom RS232-to-LAN adapter for remote control of each screen (on/off, channel select, and volume for screens using their built-in speakers). All the screens feed off a digital (fibreoptic) MATV backbone.
The function spaces have an AMX touchpanel to help set up the room for presentations. A local rack has the presentation (Panasonic projector, Sennheiser wireless system) and processing gear (Biamp Nexia, Ampetronic hearing loop) required to stage events and can accommodate an operator with mixing console if required.
Rutledge Engineering applied its experience from its AVIA-winning Melbourne Convention and Exhibition Centre project to install a dual-function network of background music speakers. ‘Dual function’ because the Bosch Praesideo system plays the roles of both paging and as a Sound System for Emergency Purposes (EWIS). The 100V line amplifiers power a rainbow nation of Bosch, JBL and TOA speakers dotted about the stadium – everywhere except the seating areas, which is the domain of the EAW system.
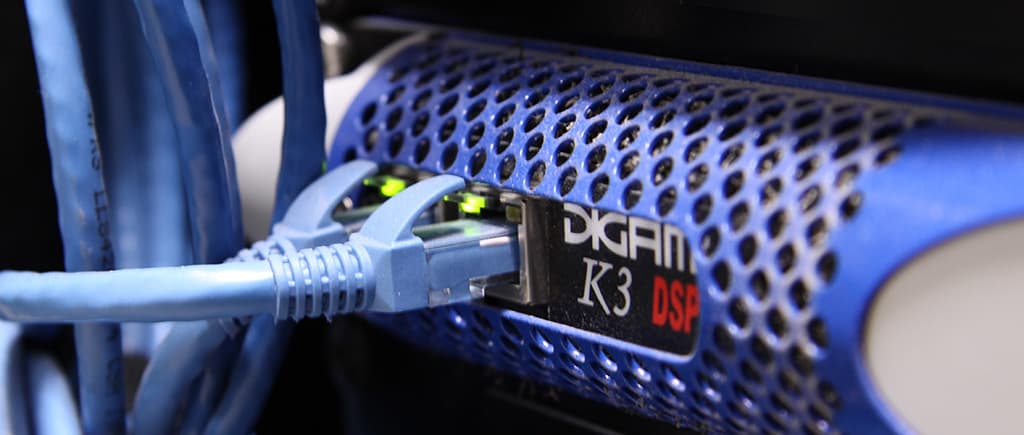
DAMPING A FACTOR
Ben Clarke: The Powersoft K3 is a touring spec amp. The benefit of using a high-spec amp is the damping control [ability of the amplifier to control undesirable movement of the speaker cone] is greater than a cheaper amp, even a cheaper Powersoft amp. When you’re driving long speaker lines you need as much control as you can over the speaker. You can adjust for EQ or level loss from running long lines but you can’t make allowances for loss of transducer control. So an amp with a high damping factor, means you can drive longer lines.
The DSP is in the amp. We’re the first to use Powersoft’s Armonia software in Australia. It allows us to use the Armonia user interface to drag in the amps you’re using, select which rack room they’re in, which speakers they’re driving in that quadrant, and set up user groups in that design, so you can dial up a configuration for a special event without affecting other aspects of the setup – Armonia makes building customisable zones and groups easy.
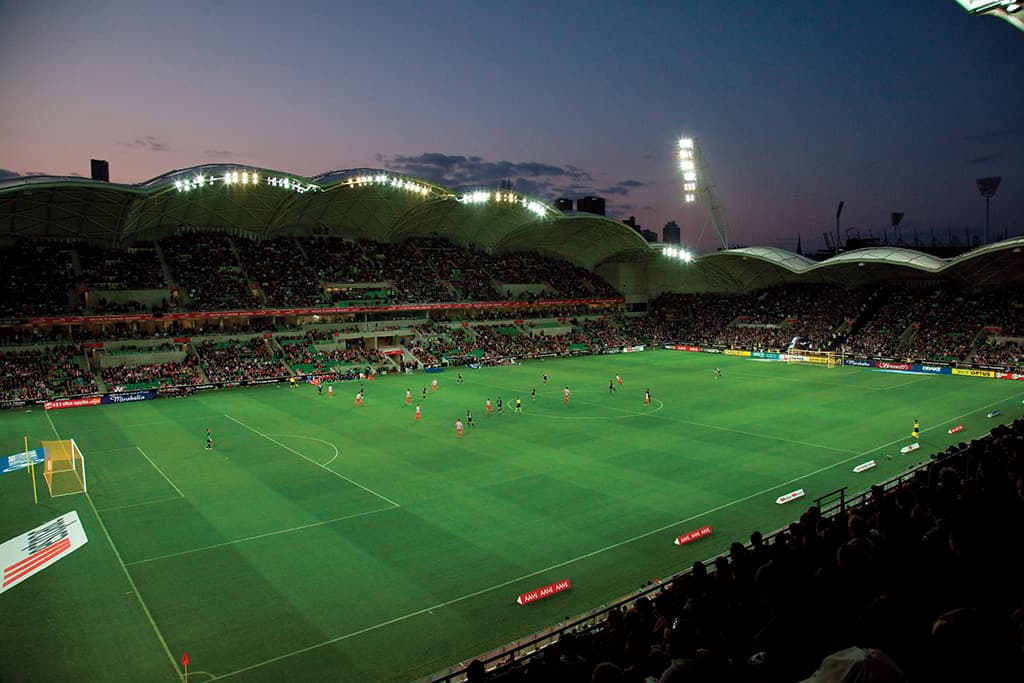
THE BOWL
US loudspeaker manufacturer EAW is well known in The States for being a big player in stadium sound – NFL and NBA stadiums and arenas are EAW’s pet subjects. Amazingly, AAMI Park is EAW’s first stadium scalp in Australia, but one suspects it’ll be the first of many.
Rutledge Engineering engaged Production Audio Services to consult on the design, and supply the bowl PA, which is based on EAW AX Series loudspeakers and Powersoft K3 amplifiers. The three-way speakers are run in passive mode, with one channel of each K3 amp feeding each AX box and letting the internal crossover do the rest. The AX boxes can be run in bi-amp mode but it was decided this was an unnecessary expense (double the amp channels, for starters).
The AX series uses a tri-ax design, with the HF device and eight-inch mid device sharing the same full cabinet-face horn, with the dipole 12-inch LF devices. This tri-axial approach has some advantages. It provides a very even frequency response across the full breadth of the speaker’s coverage, because you don’t experience the same sort of destructive interference you get from multiple arrival times from drivers spaced apart in the same box. The result is a more coherent ‘nearfield’ sound.
Production Audio’s Ben Clarke who designed the system is justifiably very proud of the results. “Intelligibility is the biggest concern in a stadium. You need to make sure you model the system as accurately as you can. We spent months in EASE exploring the options. My first priority was to guarantee the best possible direct sound to all the seats. But here’s where you can get your EASE plots to say what you like, and you have to be more discerning that that. It wasn’t simply a matter of scoring the same broadband SPL across all the seating, or getting one frequency right, the aim is to get a smooth even sound across as many frequency points as you can – the wider the frequency band, the more predictable the cluster will be.”
Ben alludes to the fact that too many stadium PAs might spec out well down to 1kHz but that’s simply not good enough: “Speech fundamentals are often below that – for example, the first harmonic of my voice is around 250Hz. So the goal is to design a system that is controlled over the widest possible band.”
But of course, the biggest issue with intelligibility in a stadium is the problem of hearing sound from speakers that aren’t right above you. Ben Clarke elaborates: “Much of the intelligibility challenge is minimising the interaction between loudspeakers from cluster to cluster, horizontally: that needs to be as tightly controlled as possible. We’re talking about multi-path reflections within the stand itself flooding into adjoining bays. That’s a big contributor to intelligibility problems.”
Not spraying sound around is a function of the loudspeakers’ directivity, which itself is a function of the cabinet size and the horn size. Thanks to the AX’s big horn mouth the pattern control goes as low as 200Hz which does wonders for keeping the sound on the punters and away from hard surfaces. “Designs fall down when they just concentrate on total SPL or direct coverage – intelligibility plots are a good way of sorting the men from the boys,” notes Clarke. (1)
FROM THE KICK-OFF
EASE plots, testing and talk mean little when 30,000 fans amass for the first big debut of the PA and, indeed, the stadium. Rogue Traders played live prior to the big match, with Norwest taking the reins of the production (providing the on-pitch supplement to the PA, designed by Justin Arthur) with Nick Macfie (from Production Technologies) providing the technical direction. Macfie picks up the story: “Sitting in the grandstand, my initial response was surprise – the sound was very ‘nearfield’, something not common in Australian stadium venues. There was a real consistency in the sound – you could wander from the coverage of one cluster to the next and it was seamless throughout. I’d go as far to say that it’s the first time I’ve heard a house stadium system capable of being properly integrated into an entertainment format, not just ground announce and replay.”
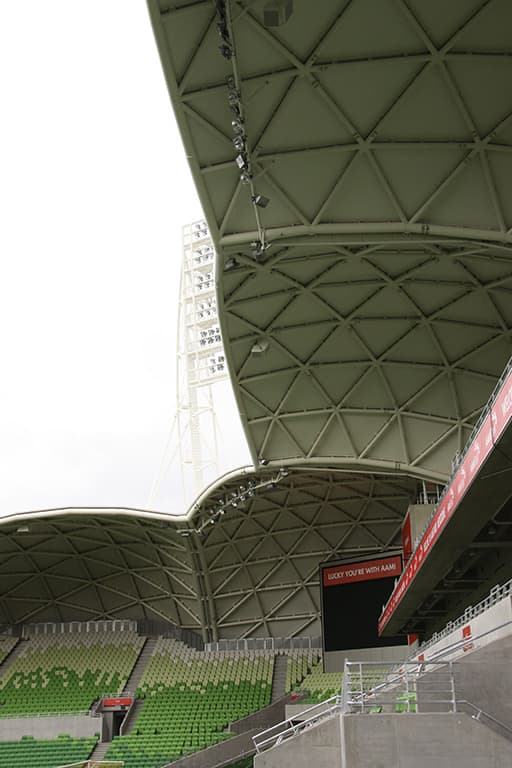
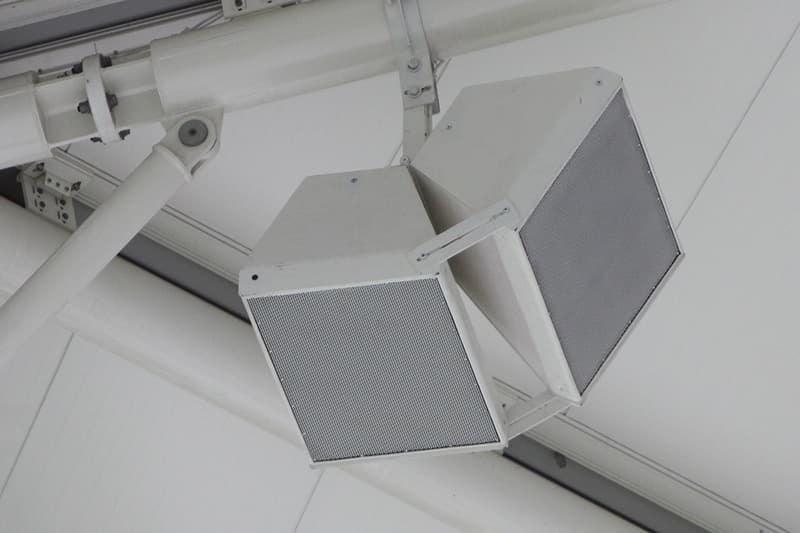
EAW AX SERIES – MUCH CHOP?
Production Audio Services’ Ben clarke explains the advantages of the EAW’s AX range of tri-axial loudspeakers.
“No matter where you go in its coverage pattern you always get the same frequency response, it’ll just reduce in level off-axis. Whereas in other designs with offset drivers you get a collapse through the crossover range where you move off the aligned axis of those transducers. That often impacts on the sound quality. Because you can only time align and frequency response of the system from a position – move off-axis, from that position (horizontally or vertically), you can get a very different repsonse. Double that when you bring in another box into the cluster – with interference between the two compounding problem.
“With the EAW AX’s tri-axial design you’re not getting that crossover collapse because it’s coming from a single point within the box. The dual 12s and the eight-inch coax mid are on a common horn, with the HF unit mounted behind the mid device. Having that point source means you always get a clean impulse – a time coherent response – without the time offset problems inherenet in a large format system.”
LIFTING THE ROOF… WITH LIGHT
When it came to illuminating the striking stadium, lighting consultants Electrolight were awarded the job of designing an artistic lighting system for the roof façade by Major Projects Victoria. Early in the design process, Electrolight’s Paul Beale teamed with fellow Melbourne lighting specialists Lightmoves to workshop ideas. Joe Casamento was Project Manager for Lightmoves and talks about his work on the stadium with a great sense of pride.
“Grocon has delivered an extraordinarily complex project – it’s an amazing structure. Electrolight was instrumental in Lightmoves being involved and we’re thankful that they turn to us for these types of projects,” said Casamento with a healthy degree of justified back-slapping.
The resulting solution was an LED node set into the intersecting roof panels. Initial plans were to use Studio Due CityLEDs, a low-voltage RGB fixture small enough to fit in between the panels. During prototyping and testing the designers agreed the concept worked, but the CityLEDs were too directional and not quite bright enough, so they set about creating a locally made alternative.
Casamento had recently completed work on the Melbourne Theatre Company building with Electrolight and local LED manufacturer Fabian Barzaghi from Space Cannon Australia which involved, amongst many other things, the development of an in-ground LED fitting. This fitting became the starting point for the roof node, as it had a shallow profile and was very bright.
“We made some prototypes and kick-started it from there. What we came up with is a custom special but we call it a Pixel P9 because it has nine Philips Luxeon Rebel LEDs in it, three of each primary colour,” Casamento explained.
Other than its brightness, the Pixel P9’s main advantage is in its special domed diffuser lens which transmits the light in all angles.
“The whole thing just glows from whichever way you’re looking at it, so there isn’t an angle you can’t see the LEDs from on the ground or in the air, which was imperative on this job. We viewed it from the top of Eureka tower during testing and it’s amazingly bright from there and close up it’s incredible,” said Casamento.
In order to decide which LED node was best for the job, all the stakeholders gathered in the adjacent Gosch’s Paddock one night for a comparison. After seeing both types of fixtures they were asked which one they preferred.
“They chose the Pixel P9 because it was brighter – almost twice as bright as the CityLED – and because they could see it from more angles,” said Casamento.
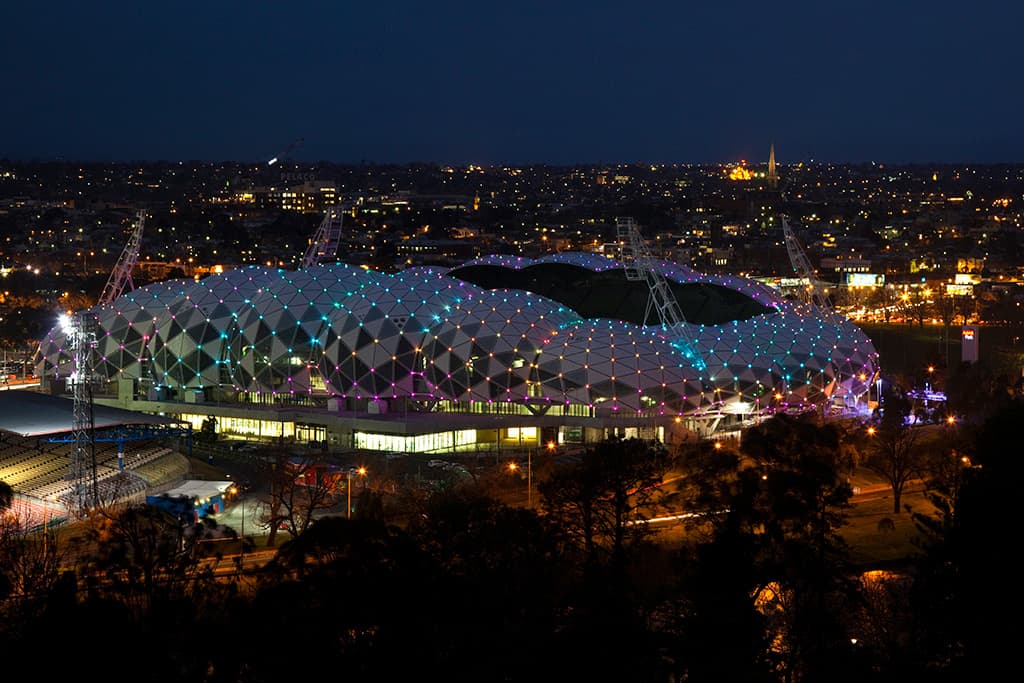
PIXEL POWER
Each LED fitting has a 200mm cable and a moulded plug and socket on each end so that the units plug into each other. Some 148 vertical runs of LEDs form the basis of the daisy chain, with each run having a feeder cable, 24V power supply and dedicated DMX.
Casamento explained the challenge of this was that each triangle on each shell was a different length as was the distance between each LED. After racking up many hours on a spreadsheet, he came up with a plan to add extension leads ranging from 2m to 8m, pre-commission each fitting of each run at the factory and provide detailed instructions for the installation team. A ‘plug and play’ approach was important as the installation was to be undertaken by abseilers who were not necessarily qualified electricians. This meticulous planning and documentation by Casamento and Lightmoves Technical Director Andrew Sherar ensured the success of the installation.
“Andrew and I spent a lot of time documenting it properly and we had all the documentation completed well ahead of the installation. We knew exactly what the bracket was, how it was going to be attached, how the runs would go, which leads to use between each LED for each particular shell. We spent months painstakingly designing and prototyping in preparation for the install so we knew we could get everything up on the roof and done in time,” revealed Casamento.
Plant rooms are located at each corner of the roof. Each has an Enttec Datagate Mk2 Art-Net to DMX converter feeding five Enttec RDS8 data splitters. A fibre line runs from each plant room back to the stadium’s central control room where the LED system is operated from a simple control widget designed by Lightmoves. The widget is used to trigger specially commissioned video content as well as an easily customisable template to allow the LED colour to be changed to complement specific events.
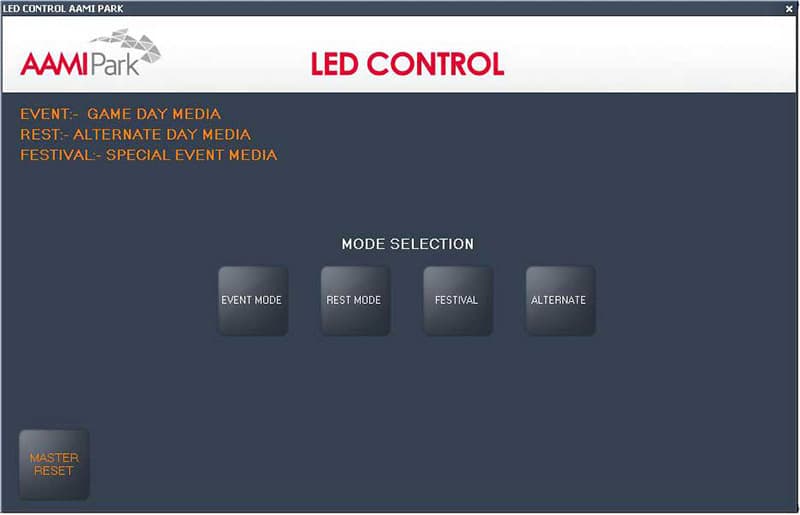

As the roof LED system is going to be used for a long time, and mostly by people with no system training and not the slightest interest in reading the extensive system documentation required in the supply contract, all control screens are simple and contain step-by-step instructions for every occasion.
BIG CANVAS
Content for the LEDs is programmed using pixel mapping via coolux Pandoras Box, effectively treating the LEDs as a 1544-pixel low-resolution video screen. Two artists have been engaged to design video content to suit the pixel mapping in Pandoras Box. Both Alexander Knox and Bruce Ramus have experience providing video media to be rendered onto LEDs – Knox’s experience in kinetic sculptures and light installations such as ‘Maxims of Behaviour’, an LED installation on Melbourne’s Royal Mail House building [see Issue 6], and Ramus’ experience in producing advanced media experiences and large-format projections for architectural and theatrical environments, made them ideally suited to this project.
“The two artists had to come up with video content to suit the pixel mapping in Pandora’s Box and that’s how we’ve programmed it. We’ve employed Lyndon Gare to be our programmer and liaise with the artists and he’s done an amazing job. Test LEDs have been set up in our commissioning room so that the artists can test their content and see how the colours render on the actual LEDs. Already there are dozens and dozens of shows – there is artwork specific for Melbourne Storm and Melbourne Victory, Australian green and gold, and each program begins with an indigenous artwork,” explained Casamento.
GOSCH IT’S GOOD
Recalling the first time he saw the finished stadium lit up, Casamento says he was lost for words.
“I remember standing in Gosch’s Paddock, seeing it come alive for the first time, it was incredible. You never forget those moments – they’re the moments that make all the hard work worth it. I consider myself extraordinarily lucky because not many people get to do projects on this scale and I’ve managed to do a couple now. I’m always humbled by the experience, and I’m so proud of this one because it’s a Melbourne-made solution for Melbournians using Victorian tax-payers’ money.”
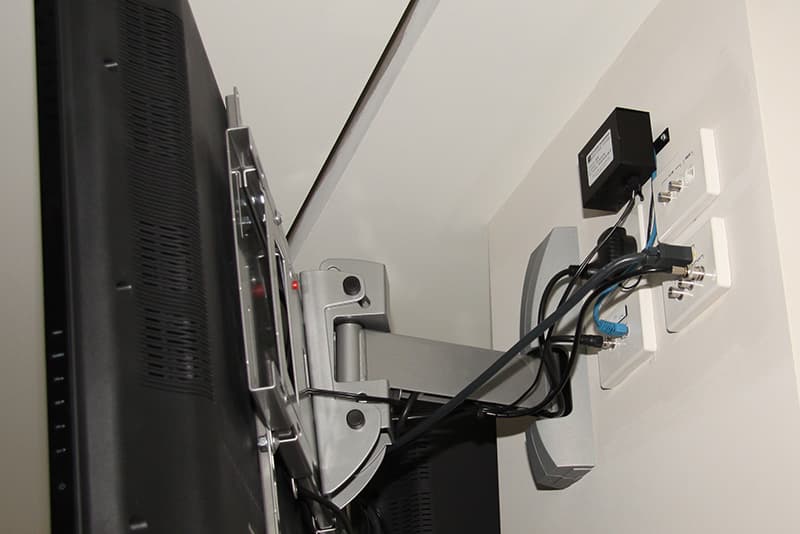
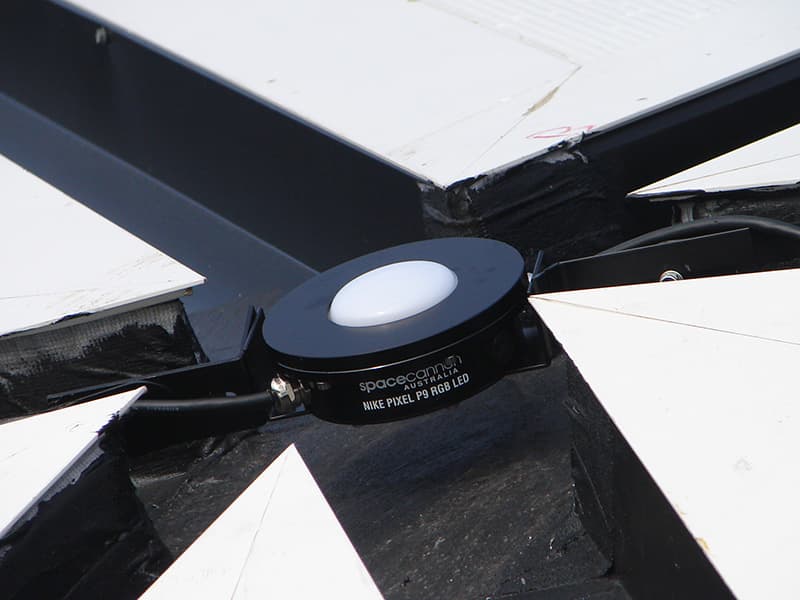
ABOUT THE PIXEL P9
Each Pixel P9 node is 130mm diameter by 39.5mm high, encased in black aluminium housing and weighs around 1kg. A custom articulated bracket was developed by Grocon in order to attach the nodes so that they’re flush with the roofline, an important factor considering cleaners and maintenance staff would have access to the roof. By placing a fitting in each panel intersection across the 20 shells, the 1544 individual Pixel P9 LED nodes delicately trace the curves and accentuate the sculptural quality of the stadium’s shells.
Fully outdoor rated (IP67), the fixtures can operate in temperatures from -15˚C to +50˚C and using a Remote Device Management (RDM) system running over DMX, thermal sensors within each node send readings back to the control room so that if ambient temperatures are outside of the unit’s tolerance, the current to each fitting can be reduced to avoid overheating. The RDM system can also provide simple diagnostics such as fixture IDs, DMX data addressing and current operating temperature.
MORE INFORMATION
AAMI Park: www.aamipark.com.au
Rutledge Engineering: (03) 9488 1500 or www.rutledge.com.au
Production Audio Services (EAW, Powersoft): (03) 9264 8000 or www.productionaudio.com.au
KLM Group (Electrical & Communications Contractor): (03) 9320 3444 or www.klmgroup.com.au
Electrolight: (03) 9670 2694 or www.electrolight.com.au
Lightmoves: (03) 9701 2500 or www.lightmoves.com
Space Cannon Australia: (03) 9486 5366 or www.spacecannon.com.au
Show Technology (Pandora’s Box): (02) 9748 1122 or www.showtech.com.au
Enttec (DMX distribution): (03) 9763 5755 or www.enttec.com
Philips Lighting (Luxeon LEDs): www.lighting.philips.com.au
Grocon: www.grocon.com.au
Major Projects Victoria: www.majorprojects.vic.gov.au
Cox Architects: www.coxarchitecture.com.au
Bosch: (02) 9683 4852 or www.boschsecurity.com.au
RESPONSES