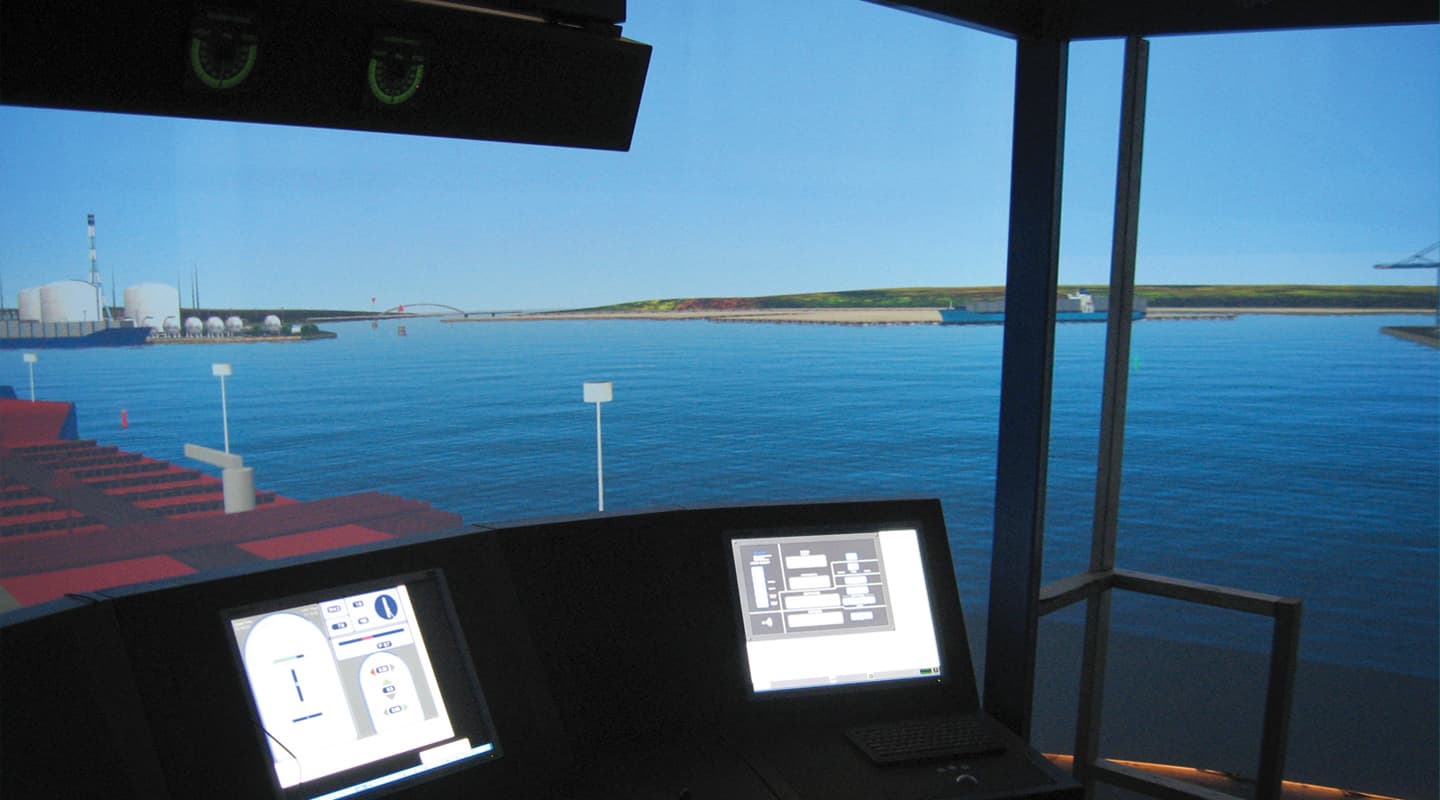
Fremantle Marine Simulation Centre
AV’s maritime correspondent visits a ship-driving school.
Text:/ Graeme Hague
Since it was only my first attempt at driving a tugboat, smashing into the wharf at a rather irresponsible five knots wasn’t a bad result. Further in my defence, nobody was hurt and nothing was damaged apart from a sizeable dent in my ego. And it was, of course, all done in the virtual world of the Fremantle Marine Simulation Centre (FMSC), and as my host Michael Brinch from Force Technology, based in Denmark, pointed out several times – under the circumstances it’s all good fun.
That is, until it gets serious – and training harbour pilots and ship’s captains is certainly that. The ocean’s shipping lanes are busier than ever before, traditional ports are getting crowded and new destinations such as the proposed loading facilities in Western Australia’s northwest are appearing all over the globe. Crews rotate through different vessels, keeping the freighters churning across the sea non-stop, but robbing the seamen of important familiarity with the ships. The professional sea captain needs more than a wooden leg, an eye-patch and foul-mouthed parrot to stay ahead of the game.
AYE AYE
Captain Rory Main, the Managing Director of the FMSC, was a captain in the Australian Merchant Navy with 14 years experience, completing his time as a Senior Officer on oil and LPG tankers. Then add to his notable CV, 20 years as a harbour pilot. He is also the president of the Australian Marine Pilots Association (AMPA) and since 2005 AMPA has been extremely active in establishing a pilot training program, even beginning with interested students at high school level, which is an innovative approach and a far cry from the traditional method of working your way up through the ranks. Main and his colleagues Raymond Alfreds and Jon Brown, who collectively add another 40 years or so of piloting expertise in harbours around the globe, saw the need for a high quality maritime simulator to allow AMPA’s vision of a training program to become a reality. Their worldwide search for the best simulators available brought them together with Michael Brinch of Denmark’s Force Technology through Force’s long-time Australian agent, Cardno Lawson Treloar.
We tend to associate ‘simulator’ with the aircraft variety, but a division of Force Technology has been in the business of recreating ships and harbours for over 25 years. While the facility at Fremantle is modest in comparison to some of the simulators they’ve built for other clients, it is nonetheless impressive, and provides a world-class training centre. From the outside, the converted wharf-side shed is unassuming, and the décor inside has so far taken a low priority, but I’m sure another lick of paint and a few pot plants aren’t far away. However, there’s no question about the quality of the computer technology and audiovisual equipment that run the simulator.
RE: PORT
Once the installation is complete there is a subtle shift in the relationship between FMSC and Force Technology as Captain Main can potentially commission from Force and Cardno Lawson Treloar additional scenarios or port models according to client demands. Aside from AMPA’s pilot training agenda there are basically two approaches to the requirement for a simulator. The manufacturer or owner of a particular vessel may decide on virtually mimicking their ship to train crews comprehensively on all its performance characteristics before anyone even gets a whiff of salt air. They can also request that the simulator’s database include projected destinations and weather conditions. With vessels worth tens of millions of dollars it makes sense. Conversely, a port management authority may introduce a policy that no pilot or captain can navigate into their harbour without having passed a simulation test that acquaints them thoroughly with the hazards of the port. The smallest mishap can stop the docks operating and cause a massive loss of business.
However, any training in a simulator is at risk of amounting to nothing, if the experience isn’t real enough. The crews have to be taken out of their comfort zone and forget they’re inside a shed. For all their expertise in ‘simulation and information technology’, plus the software encoding and audiovisual equipment (Force Technology’s headquarters employs nearly 1000 people with an annual turnover of $217m) the company’s primary product here is illusion – and very convincing illusions at that.
(above) Bridge A has a 200° field of view projected onto an 8m cylindrical screen.
Photo: David Aubourg.
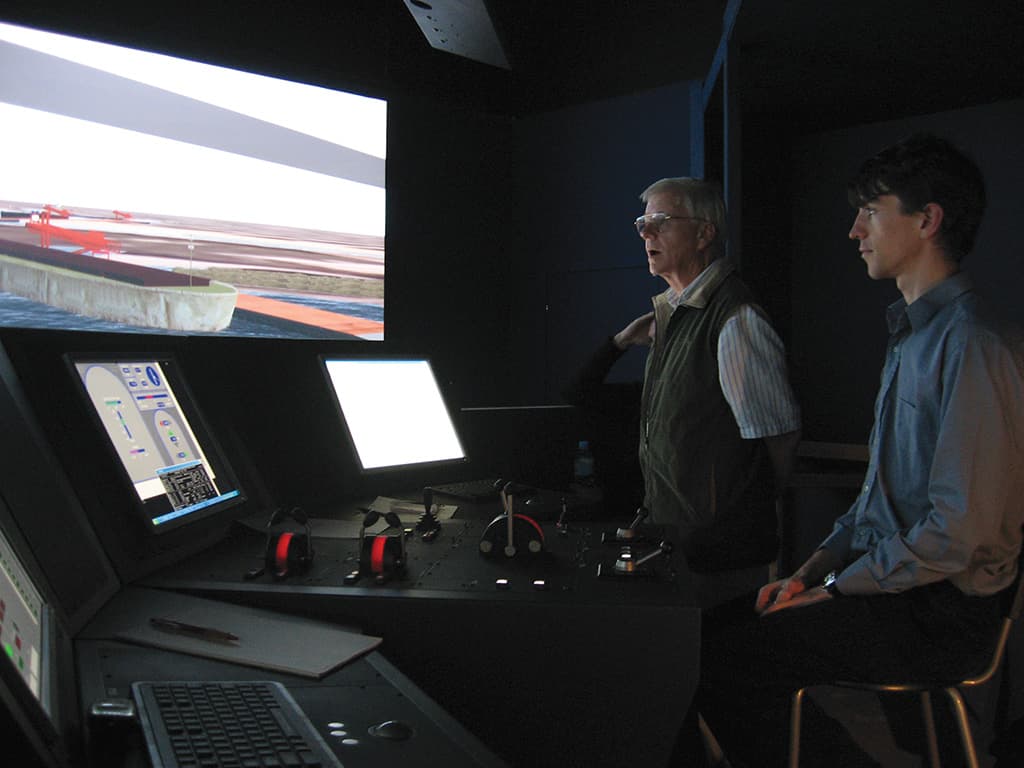
David Taylor of Cardno Lawson Treloar, Perth and Pilot Rob Dawson of Port Headland Pilots on the 120° field of view Bridge B.
Photo: David Aubourg
LET THE GAMES BEGIN
When we first arrived Captain Main was running a demonstration of one of the two simulators and there was a moment when I wasn’t sure it was polite to follow Brinch inside. Standing halfway in the door and seeing the simulation being played, I’ll confess I took a hasty step backwards and checked I wasn’t walking onto a moving platform – some kind of hydraulically operated deck that moved in conjunction with the simulator. But no, it was solid floor. The sensation of entering a ship’s bridge with the vessel dipping and rocking on the waves was purely created by a projected vision onto a large curved screen. Startling, really.
FMSC commissioned two linked simulators which are run by a master station and Force Technology’s proprietary SimFlex Navigator software. Data from SimFlex is manipulated by a CompactUTM image processor from 3D Perception in Norway that handles image distortion and blending for the multiple projectors and curved projection surfaces. Each projector is then driven by a dedicated computer networked with the CompactUTM.
Force Technology’s engineers are on the cusp of developing a software graphics engine that will replace the external CompactUTM processing unit altogether, and, according to Brinch, recent improvements in CPU and GPU performance may allow several projectors to run from a single standard PC.
The smaller of the simulators uses three Optima EP1690 DLP projectors focused onto individual flat screens to create 120˚ of vision. The more sophisticated second simulator uses five wide-angle 3D Perception CompactView SX+21-TY projectors on a 200˚ continuously-curved screen. The warping and blending of the five images on to this screen is truly stunning. You’re presented with a three-dimensional panorama exactly as you’d see from the bridge of your ship. If you make a turn to port or starboard the vision swings perfectly through the arc, plus it incorporates any vertical movement the boat might perform. In our case, we were still on the tug boat, so there was a fair amount of list in the right direction and I unconsciously leaned the opposite way. Next Rory performed a ‘crash stop’, which had the bow wildly plunging downwards – and yes, both myself and the other guests desperately grabbed for the handrails. It’s a source of constant amusement for Brinch and Main to see newcomers swaying about like drunken sailors in response to the boat’s movement when, in fact, the floor isn’t moving at all. Bloody funny, apparently.
SIMFLEX-ITY ITSELF
The master SimFlex server allows the two simulators to operate independently or competitively. For example the smaller simulator could have a tug boat loaded into the system, while the five-projector system will have the cruise liner that requires berthing by the tug – or maybe a second tug. Both screens are displaying the same environment and the simulators respond to each other’s actions, plus any additional parameters demanded by the master station such as weather, tide and visibility. The visual quality of that environment is dependent on the client’s needs as they specified early in the process. Reproducing local weather is very important – a given in fact – as is accurately portraying the topography of the location – the size and shape of the harbour and its approaches. Then it requires the correct berthing points including to-scale wharfs, jetties, pontoons and buffers, navigation markers and buoys, and anything else critical to a pilot’s recognition of where they are and where they want to go. Careful work goes into the recreation of this content, because it’s vital that a genuine perception of depth-of-field and distance is achieved. Beyond this things can get a little more bland. If a model of Sydney Harbour was needed you’re not going to see your mum’s house on the Manly foreshore, but the Opera House and Harbour Bridge will no doubt get a mention. If the client does require a specific landmark that perhaps wouldn’t be included, they merely need to ask.
Building these models is a painstaking task, involving thousands of photographs, aerial surveillance pictures and up-to-date maps. This is where Force Technology’s relationship with Carndno Lawson Treloar, with their vast experience in hydrographical modelling of Australian waters and ports makes a big contribution to the data collection process. Every effort is made to ensure their models won’t be abruptly rendered obsolete by circumstances beyond their control – nobody bulldozes the Opera House a week after they finish modelling – otherwise they attempt to update information that affects navigation as quickly as possible.
“”
It’s a source of constant amusement to see newcomers swaying about like drunken sailors in response to the boat’s movement when the floor isn’t moving at all.
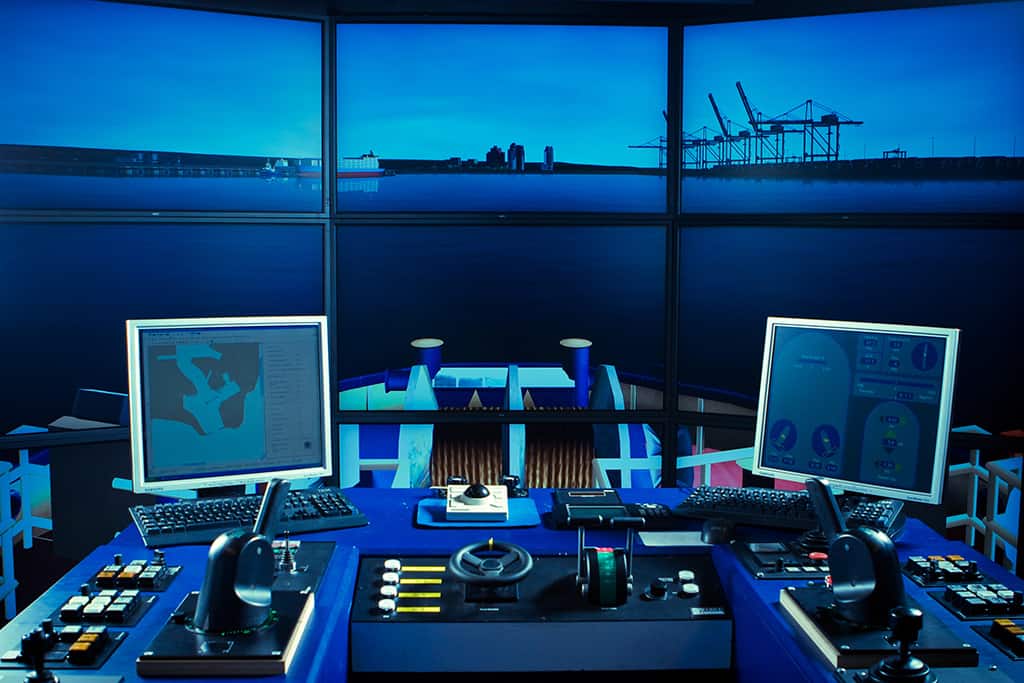
A top of the line SimFlex Navigator bridge with a full set of handles and interfaces.
Photo courtesy of Force Technology
UNDER CONTROL
When it comes to simulating specific vessels, Force Technology have wind tunnels and flotation tanks in Denmark. They can create scale replicas of the craft and conduct real-world experiments that gather information that may not be picked up in computer modelling. If a client requires, they can replicate a ship’s bridge and controls. At FMSC the simulator consoles offer a more generic surface with a focus on tugboats and pilot craft, these being the kind of clientele they expect initially. A centre section of thruster, rudder and speed controls, with a digital display for each is flanked by a (I have to say, very cool-looking) working radar on one side and a monitor for external cameras on the other.
For the fully-programmable weather the simulators display it as it should be. The waves are the correct size according to what’s causing them, and come from the right direction – complete with whitecaps, if the wind is strong enough. Swell and tidal surge can also be introduced. Visibility can be degraded by rain and mist. Shadows, glare and reflections are all reproduced. All these elements are factored in to affect the ship’s behaviour and the operator’s perception of what is happening.
Which takes care of the visual side of things. That’s only a part of the necessary illusion. Rory Main draws a line at tossing buckets of sea water over his trainees and leaving a smelly dead fish somewhere, but audio is another thing altogether.
DIGITAL SAMPLES
Force Technology use a vast library of digital samples to create environmental sounds and authentic engine noises that respond to the ship’s controls. If these aren’t enough Brinch isn’t beyond doing his best ‘Leonardo Di Caprio on the bow of the Titanic’ impersonation with his trusty Edirol recorder and collecting samples himself. It’s all in the interests of keeping things real. Sound in the simulators is delivered by a 5.1 surround system, and when you consider that each effect must come at the right time, at the right volume, and from the right direction, you realise it’s a rather unsung, clever component of the simulators. A subwoofer somewhere even vibrates the floor (sorry, ‘deck’) when the engines were suddenly dumped into reverse.
After experiencing the simulators you’d expect to be shown a Cray-like supercomputer feeding it all from a hermetically sealed room. Instead, a rack of new – but quite unremarkable – Dell PC’s are running the show, and the air conditioner in the corner has seen better days. Even the graphics card for each, albeit a GeForce 8800 series is a commercial off-the-shelf product. The projectors aren’t anything special either. The size of the screens are determined by the client’s requirement and after that it’s quite a straightforward formula of figuring out how many projectors are needed. The secret ingredient for the simulators really lies in the SimFlex Navigator software, which operates comfortably under Windows XP. It allows the company to offer desktop simulators that can run on any computer, or like the upcoming monster on Brinch’s order book, with 360˚ vision and 4m-high screens. The network systems like FMSC’s are constructed and extensively tested in Denmark before being transported to their destination, but most of the ancillary equipment such as projectors and screen material can be sourced locally. The usual attention is paid to optical cable runs and avoiding interference so the screens stay crystal clear. Backup of data is also a fairly run-of-the-mill procedure, while redundancy is almost non-existent. If there’s a power blackout, it’s off to Freo’s favourite, the Sail and Anchor pub, for a beer until it comes back.
The emphasis for this kind of simulation training isn’t really about avoiding tragedy, although a recent incident involving a cruise ship in the Antarctic illustrates that serious accidents are still possible. Rather, it’s about preventing mishaps like mine when I smacked into the wharf, or when a ship strays out of a channel and runs aground. Nothing actually sinks and no one drowns, but heads will certainly roll. These nautical equivalents of minor fender-benders cost millions of dollars – ship panel beaters don’t come cheap. More companies are recognising that investing money into simulation training for crews are dollars well spent, because bigger ships, more destinations and crowded sea lanes are reducing the margin for error.
THE REAL THING
The Fremantle Maritime Simulation Centre is a lot of fun – Rory Main’s son is banned from entering unless he hands over his Warcraft installation DVD first. The simulators themselves are a great display of audiovisual magic and an interesting example of what ordinary hardware can do when it’s driven by clever software. It’s easy to forget there is a serious business behind it all.
RESPONSES