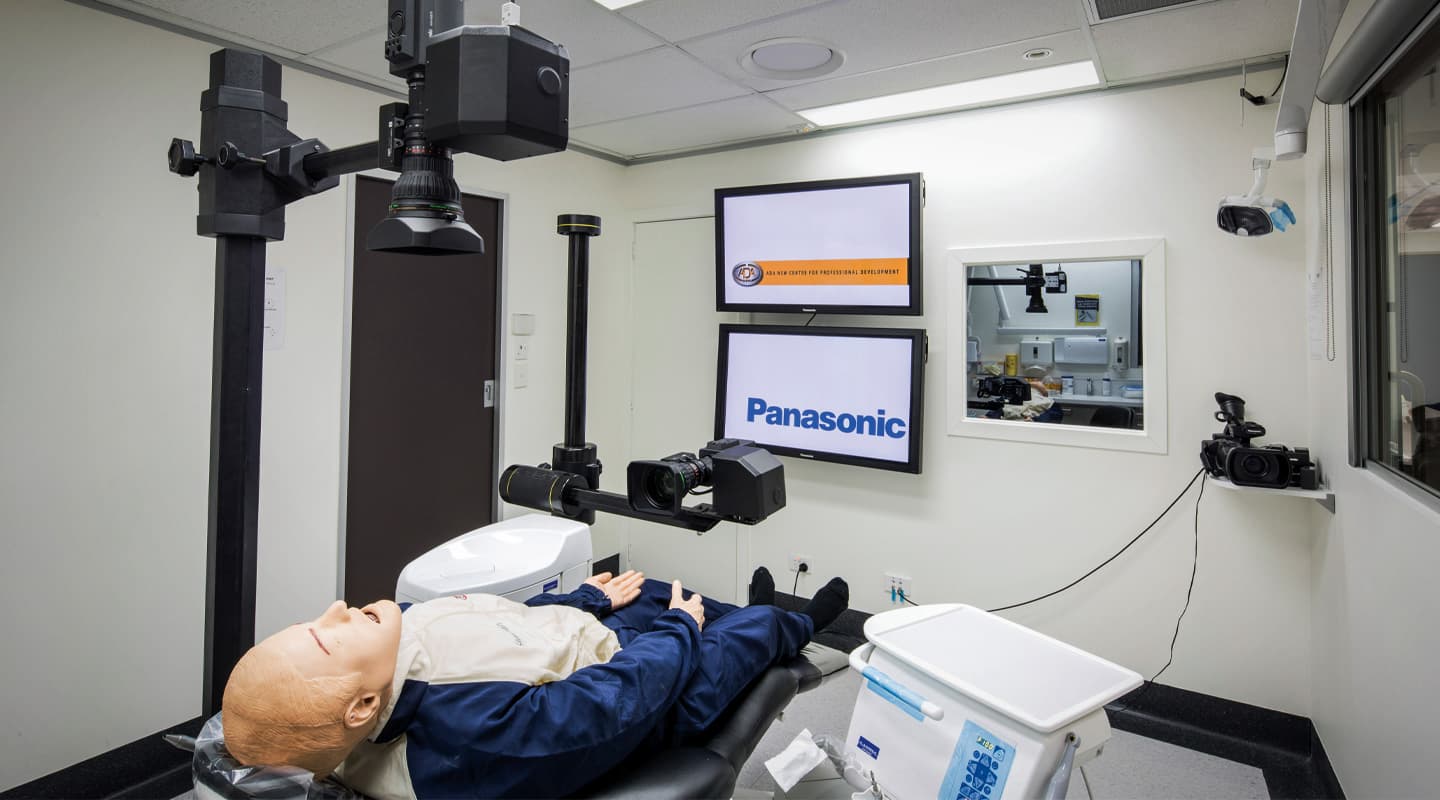
Knowing The Drill
The NSW branch of the Australian Dental Association is really sinking its professional development teeth into AV.
Text:/ Andy Ciddor
It’s reassuring to know that Australian dentists are now required to regularly brush up on their skills to stay registered, just like a CTS, CCNA or a chartered engineer. However, years before it became mandatory, the NSW branch of the Australian Dental Association (ADA NSW), always a strong advocate of continuing professional development, had set up the Centre for Professional Development (CPD) for its members. It’s the peak training body and provider of continuing professional development to several thousand NSW dentists and ancillary dental staff such as hygienists and assistants.
Each year, over 4000 people receive training that ranges from hands-on courses run in its clinical training centre, to dental events run off-site using teaching material produced in house. The AV department, a separate business unit that works under the name Best Practice Productions (BPP), is an integral part of all CPD activities, even having an event management unit which manages the logistics for in-house events as well as managing all off-site events which include some big conferences and conventions each year.
THE WHOLE TOOTH
However, the mainstay of CPD’s activities are the hands-on clinical courses run in the dedicated clinical training centre where there are 20 clinical training workstations, each equipped with the full range of facilities such as drills, suction, air and water, found in a contemporary dental surgery. At the front of this room is one of Panasonic’s 103-inch HD plasma panels to allow the trainees to see the instructor demonstrating in the nearby surgery facility.
“I’d thought I had dealt with some pretty demanding presenters in my previous career in corporate AV production,” admits Brett Tyler, BPP’s Production Manager, “but I have come to understand that the medical industry demands the highest standards for detail and colour accuracy. A big part of the AV system in the clinical training centre is the 103-inch Panasonic plasma. The colour correctness and the brightness we were able to achieve in that room and still be able to have light for people to work is the key to its success. Certainly there are projectors out there that would meet the requirements for resolution and contrast ratio, but only if the room was completely dark. It’s not a theatre; it’s a clinical training centre, so delivering the image quality required – with high ambient lighting is an important part of getting the AV right.”
In addition to the clinical training centre, there is a 100-seat lecture room equipped with a 130-inch projection screen and PA system, and there are four surgeries in the facility, each with a different focus. One is media focussed, fitted out with HD cameras, while the other three are equipped with specialised equipment such as high-resolution microscopes and panoramic X-ray machines, which feed vision into the central Black Magic Smart Videohub 16 x 16 matrix.
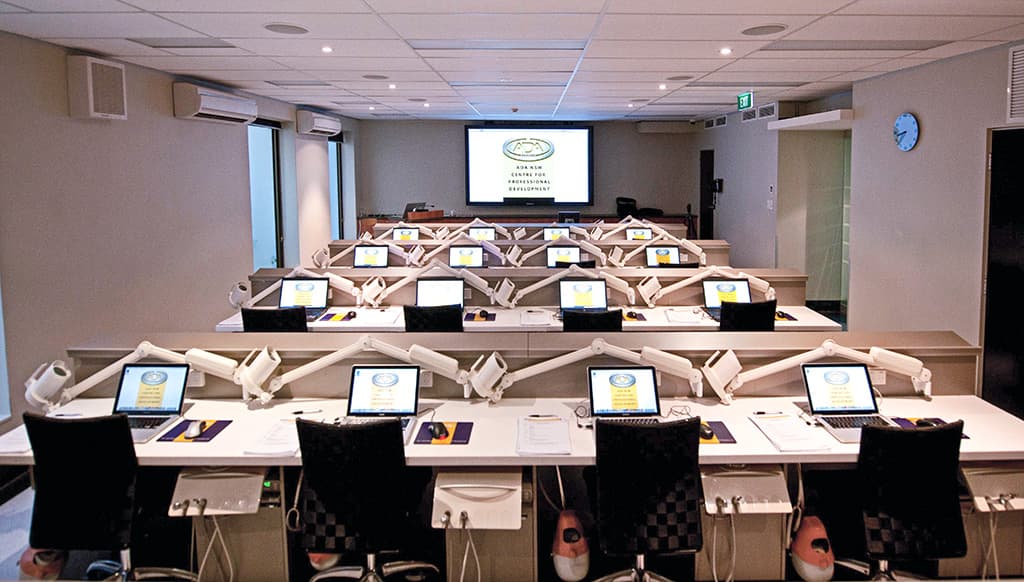
BRACING FOR CHANGE
Tyler has spent the last couple of years designing and implementing a full HD digital system for the media surgery to replace the standard definition system that had been expanding and acquiring upgrades for the last decade. Despite the dental instructors’ insatiable appetite for higher-detailed and more accurately coloured images, the main reason for the upgrade was the long-term ability to sustain the required levels of high availability on a system employing devices where parts availability and maintenance services were on the wane.
He explains the new setup: “The fitout is currently five full HD cameras. We’re using industrial box cameras, fitted with what are essentially ENG lenses to get the servo zoom and focus, together with AMX PTZ (pan/tilt/zoom) heads. We’re able get the combination of zoom, low-light performance and depth of field necessary to capture the required detail. The human mouth is a very, very specific production environment. It’s got any number of challenges, not least of which is that the clinician usually likes to lean their head in – quite rightly with what they’re trying to do – and drill or suture or cut or whatever, and that will often put their head between the camera and the action. The ideal camera shot can be obstructed by the dental instruments, suction, the clinician’s hands, the dental assistant’s hands and of course – the patients lips.
“We have very specific requirements for how close the camera can be for the comfort of the patient and for infection control. We have to keep the cameras outside of the infection zone, which is approximately 800mm from the patient’s mouth, otherwise we’d need to clean the lenses with stuff you just wouldn’t put on lenses. That, coupled with the fact that we’ve got to be out of the way of the clinician. But then there’s the zoom requirement for getting in to capture the required detail. We lose at least a stop or two of light with the lens doublers, which makes the balance of getting enough depth of field very difficult.
“The broader trend in the market is to go for larger sensors, with their shallow depth of field, to get that filmic look. So there are some challenges in replacing the standard definition cameras that have been functioning here for seven or eight years which had much smaller chips. We were quite lucky that the light sensitivity has improved so much over the last eight years of sensor technology that we didn’t really lose any depth of field, but we’ve managed to gain resolution.
“Another factor which complicates matters is that when it’s a surgical procedure we have surgical operatory lights and we can just flood the whole mouth with plenty of light and it becomes quite easy, because we get a lot of depth of field. But more than half of the restorative procedures that are taught in dentistry today use materials that are hardened by light. So it’s just not an option to flood the mouth with that much light. We have to deal with a very fine balance to get the necessary level of detail.”
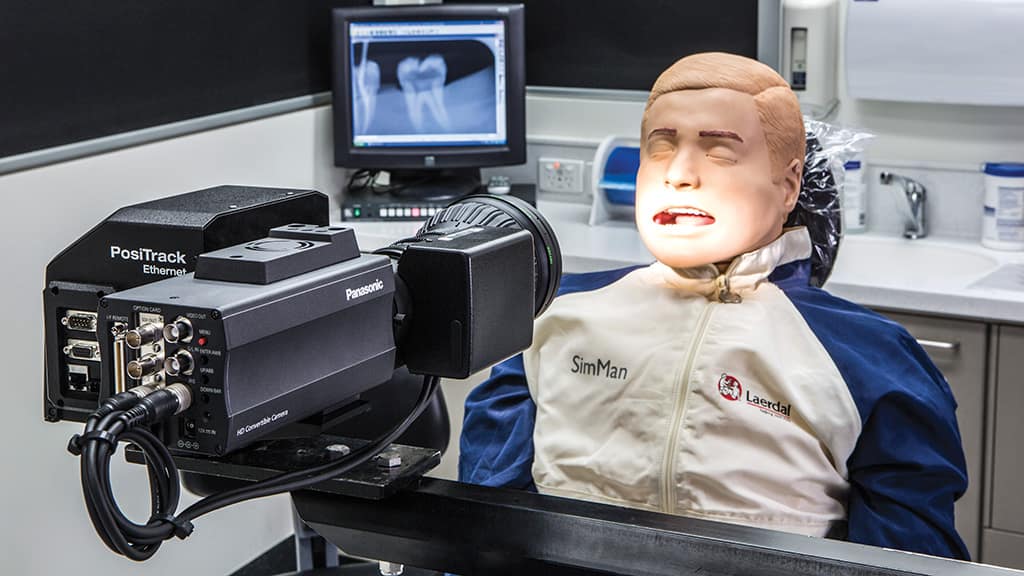
FILLING IN THE PAST
In designing the HD replacement system Tyler had the advantage of being able to learn some very valuable lessons by looking at the collection of abandoned equipment that had been tried in the past. “The HD system was designed in-house at a point where I’d been working with the company for nearly two years,” explains Tyler. “It took that long for me to get my head around the previous system, which was the result of a long process of trial and error over about eight years. It was a mix of standards and formats going back to S-Video. I saw the remnants of things that had been tried and thought to myself, ‘You know what? As an integrator I would have tried that too.’ Ultimately what we were left with was the stuff that worked and that was quite helpful to me in the process of designing a new system, because I knew what things not to try. It was technical evolution in the Darwinian sense: only the ideas that worked, survived; and I was lucky to have that as a basis on which to design the new system.
“The majority of heavy lifting in terms of getting the right picture in front of our participants and trainees was done by the lenses and solving that very fine, multi-variable equation of how do we get close enough, zoomed-in enough and then minimise the vibration from people walking on the floor had already been done. It’s so zoomed in on that level, that flies mating on the wall would shake the image.”
PANASONIC PARTNER
By the time Tyler had added some additional capabilities to those offered by the previous system, he realised that what he had on his hands was going to be quite a complex design. To simplify the integration and commissioning process, they decided to source as many components as possible from a single manufacturer. Having had a really good experience with Panasonic during the process of installing and integrating the 103-inch plasma screen into the existing system, and after looking at Panasonic’s wide spread of products across a range of markets, including such things as security cameras and controllers, prosumer equipment, professional AV and all the way up to the high-end of broadcast, Tyler decided to give them a try.
“We made an approach to Panasonic, saying this is who we are and what we’re doing. This is the system we’re replacing, and we’ve already done most of the design work, so what we’re looking for is a partner who will give us tech support and pre-sales support by vetting the design and saying, ‘Yes we can ensure our products will work in a particular way.’ And that’s precisely what happened, so we proceeded with an agreement with Panasonic through its distributor Lemac.
“After their site visits, Lemac and Panasonic were so impressed with what we were trying to do, they jointly decided to form a partnership where they were able to provide the support that we required in exchange for us becoming a reference site. They felt it was unique, and something they wanted to have in their portfolio of cases. From there the process was basically a phased procurement of gear so that we could test and confirm individual components of the broader system.”
OPEN UP & SAY A-HA
Using this approach the BPP team took on the systems integration, only calling in AT Controls to program the AMX control system that automates the operation of the PTZ and camera systems. Tyler again:
“AT Controls had some really clever coding and logic solutions to what were ultimately real-world physics and engineering problems. I think the best control system programmers are those who understand the human operator as well as they understand their code; knowing which human errors are the most likely, before the human does, and coding accordingly. We’ve got a very polished, truly integrated result now, and a big part of that success is the AMX programming.
“We’re really pleased with both the hardware and the image results we’re seeing, but I’m also very pleased we got a very workable result, to the point where despite our system being more complex than the one we replaced, yet we’ve actually been able to down-skill the operator. This gives us the flexibility to have more people trained to operate the system. That alone has commercial value to our business.”
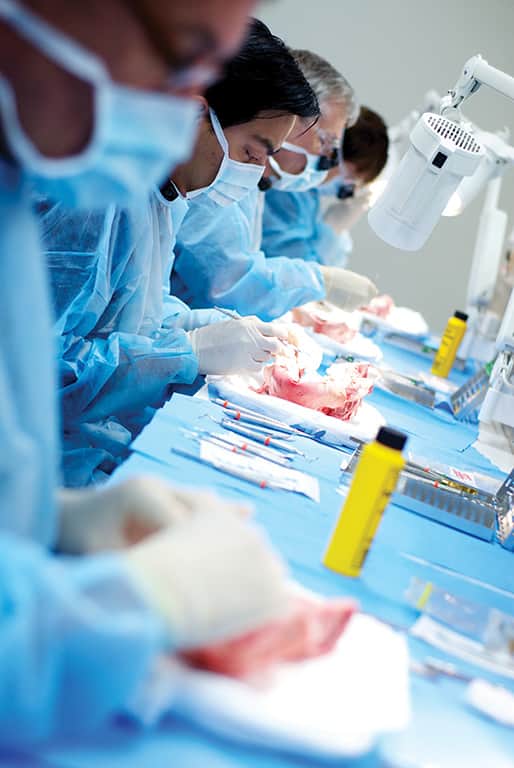
“”
The human mouth is a very, very specific production environment
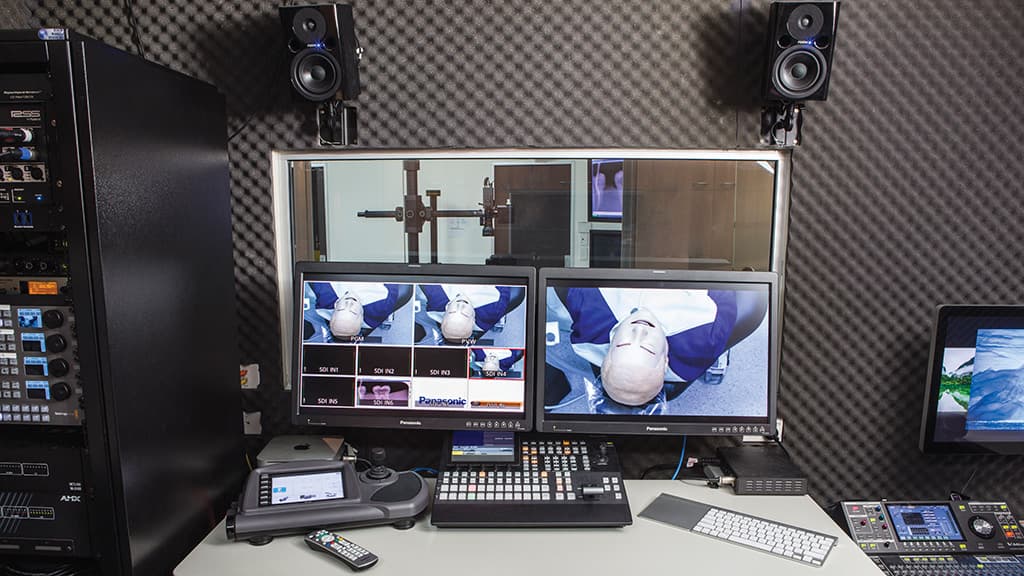
CAPTURE & DISTRIBUTION
In addition to the upgrading of image acquisition quality, great strides have also been made in the areas of audio capture and distribution and image recording distribution and workflow. All images are scaled to 1080i at the edges of the network allowing the 16 x 16 video matrix to route any image to any place including the Black Magic Design Hyperdeck Studio recorders. This allows iso (clean feed) recordings to be made from every camera during a surgical session in addition to the switched mixer output, and, coupled with the recent addition of the Pro Res (HQ) codec support to the Hyperdeck, simplifies post production workflow into the Final Cut Pro pipeline. The scalers also enable the BPP team to easily capture such elements as laptop slideshows from lecturers who may be presenting to small groups in minor presentation spaces.
AURALLY ORAL
The initial design approach for a sound system offering similar flexibility and capabilities as the video system was to use a similar architecture and employ a DSP-based matrix system with some echo-cancelling and digital delay capacity. However, after some discussions with the more audio-oriented members of the BPP team, a Roland M-300 desk digital desk with digital snakes and a selection of REAC I/O modules was selected. This provides an automation interface to the AMX system, together with simple and flexible placement of inputs and outputs in each of the surgery and presentation spaces along with sophisticated record and playback capabilities. With a further level of programming the M-300 was also persuaded to provide an IFB (interruptible fold back – i.e. production comms) system to the clinicians/presenters, camera operators and other production and floor crew.
In production, the entire surgery/studio presentation system is driven by the ‘director’ from a seven-inch AMX touch panel which allows the operation of the camera PTZ systems and triggers the vision mixer and audio mixer. There are ceiling-mounted PTZ cameras in the surgery studio and presentation spaces to allow the trainer to be seen by and communicate with the course participants, and there are microphones at both ends of the network to allow for presenters and participants to engage in Q&A sessions.
BEST PRACTICE
In addition to the full post production facilities for packaging of all kinds of sessions for delayed presentation and delivery of pre-recorded materials, the network tails for the CPD have been beefed up to a respectable symmetrical 20Mbps for future live streaming and remote presentation sessions.
After years of providing a service to those of its members that wanted to participate in continuing professional development, the NSW ADA through its CPD is gearing up for a surge in demand for their services as dentists throughout the country are now seeking such training. It looks like it’s going to get even busier for the folk at Best Practice Productions.
KEY PROJECT PARTNERS
Panasonic Australia (Pre-sales Design & Engineering Support): www.panasonic.com.au
Lemac (Supply & Engineering Support): www.lemac.com.au
AT Controls (AMX Programmers): www.atcontrols.com.au
ConferencePoint.com.au (Installers): www.conferencepoint.com.au
EQUIPMENT LIST
CAMERAS
2 × Panasonic AW- HE870, with Fujinon Lenses mounted on AMX PTE-300 PTZ heads
3 × Panasonic AW-HE120 PTZ
1 × Panasonic AG-HPX-250
CAMERA CONTROL
AMX NXP-PLV
PRODUCTION SWITCHER
Panasonic AV-HS410
VIDEO MATRIX SWITCHER
Black Magic Design – Smart Videohub
CAPTURE
4 × Black Magic Design Hyperdeck Studio.
2 × Black Magic Design Analogue to HD-SDI audio embedders
SIGNAL PROCESSING
3 × Kramer Electronics VP-729 presentation scaler/switches
DISPLAYS
1 × 103-inch Panasonic plasma TH-103PF12W
2 × 42-inch HD Panasonic
1 × 130-inch 16:9 projector and screen
AUDIO EQUIPMENT
Roland M-300 digital mixing console
VIDEO CONFERENCING
Panasonic HDVC High Definition codec (3D capable).
AUTOMATION & CONTROL
1 × AMX NI-3000 processor
1 × AMX NI-4000 processor
2 × AMX NI-700
2 × AMX ATV-PC2 Dual Power Controllers
CAMERA MOUNTS
Manfrotto ‘Skytrack’ ceiling mount system
RESPONSES