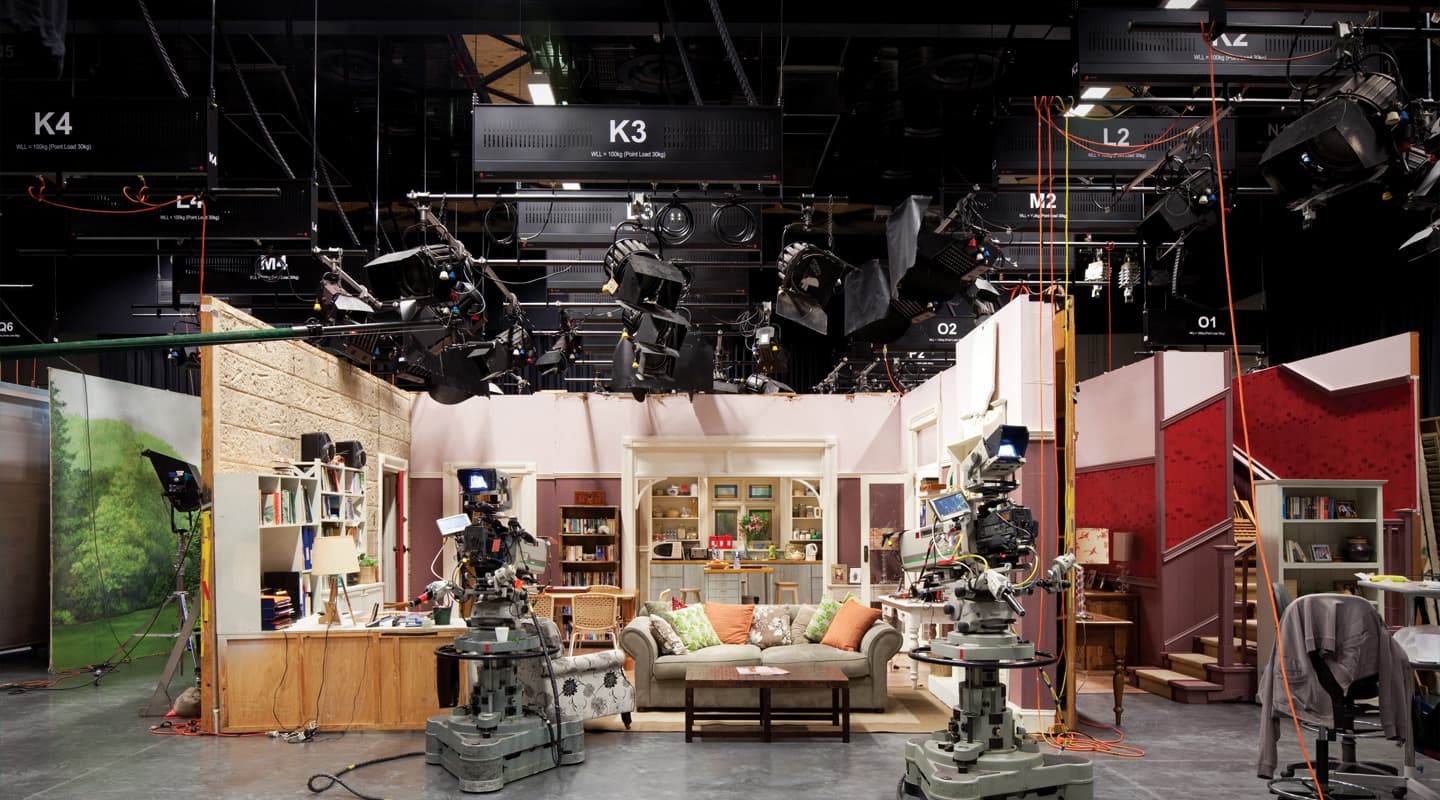
Seven Keeps it Simple
Slick, sophisticated, and huge – that’s the new TV lighting rig at Seven.
Text:/ Tim Stackpool
Photographer:/ Steve Back (steveback.com.au)
The lighting rig at Seven Network’s two new drama studios in the Australian Technology Park’s Media City facility is arguably the most sophisticated and largest television lighting haulage operation in Australia. It’s an easy claim to back, considering the 48 dimmer racks, 96 hoists, and matching lighting battens that form part of each studio’s installation. The whole system is the result of the combined expertise of Seven’s engineering department and Jands Electronics, which won the contract for the project. Part of a four-studio complex at Media City, the two studios were constructed primarily to meet Seven Network’s commitment to local production. As such the facility is purpose built for the network’s present requirements, although a certain level of future-proofing adaptability is in-built.
ALL THINGS TO ALL ENGINEERS
“The key element of the brief from Network Seven was simplicity and ease of maintenance,” reveals John Buckley, who managed the project for Jands. “It would have been possible to have installed a more sophisticated batten control system with additional capabilities such as memories and presets, for example, but that would also have increased the need for training and management of staff operating the studios day to day.”
Designed for maximum flexibility, the new studio’s basic building was constructed so a client can fit it out to suit their production needs. For Seven’s production of television dramas, specific operating principles allow for fast and efficient set and lighting turnovers through a floor-operated system. This system allows bars to be loaded in the fully-extended position down on the studio floor and then raised to clear the space for the arrival of sets and scenery.
Each studio is fitted with 96 of Jands’ brand new SLX 100 hoists. Built in partnership between Jands and ASM Steuerungstechnik of Germany, this dual-band hoist has a lifting height of eight metres and a load capacity of 100kg.
Seven provided all the lighting fixtures from its now-closed Epping facility, which included riches from 50 years of production. The oldest fixtures on site were used for Rip Tide in the early 1960s. Mostly, however, the network elected to transfer the Quartzcolour fixtures that had been purchased when Australia converted to colour television in 1974. “There was an enormous inventory of fittings to choose from, based largely on the fact that when colour TV started, illumination was typically 1500 lux compared to more like 800 lux today,” explains Buckley. Initially, each studio has been provided with 380 tungsten fittings ranging from 1kW to 10kW; both fresnel spots and softlights.
Back to the future at Media City. ATN7‘s brand new drama studios feature state-of-the-art dimmers, hoists and lighting battens alongside battered 1970s Vinten camera pedestals and rusty 1970s luminaires.
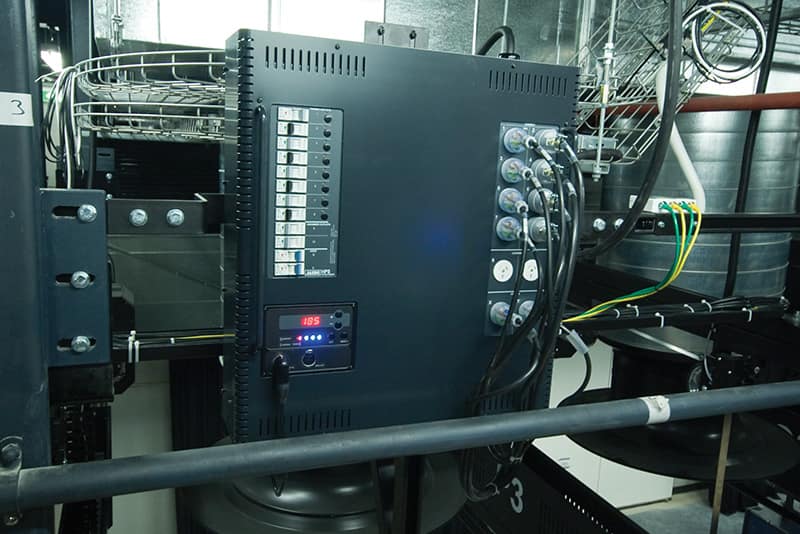
While not strictly having to be all things to all producers, the challenge of versatility did need to be addressed. The project was specified to deliver a base capability, plus an overlay for the many and varied users. With this in mind, there were always going to be challenges of time, capability, and cost. To overcome these hurdles, the Media City and Jands project team had to marry the project to an existing master building project through the builder, Watpac. Jands provided all the Seven Network requires to satisfy present needs, while future-proofing the system, allowing it to be modified when the need arises.
Along with techs from Seven, two mechanical crews from Jands and two electrical subcontractors – Lancet Electrical for controls and Bass Electrical for power reticulation – made up the team, with technical wiring assistance from Image Devices. Acoustic advice came from Marshall Day Acoustics. In all, 35 staff were inducted for the project, including engineers and project management staff. Jands had a crew peak of 16 staff on site for about three weeks.
As always, external and internal teamwork was key to the overall success of the project. Expertise at operational, mechanical, and engineering levels in setting the framework for the design was provided by Seven. These skills then had to be integrated with the brief to give Jands a clear scope of works that remained constant throughout the project. In essence the client and facilitator both knew what was required and how best to achieve it.
JUST THE FACTS
Dimmers
48 x Jands HPX Custom Dimmer Racks c/w 4 x 2.5kW & 4 x 5kW dimmer channels.
Lighting Control
Compulite Micro 4D (relocated from Epping facility)
Hoists
96 x Jands SLX 100 Band Hoists
Lighting Battens
96 x 4-circuit lighting battens, 2 x 10A and 2 x 20A, plus future wiring for Ethernet and composite video/ SDI.
Hoist Controls
Remote control of up to 24 hoists as a group together with linking capacities to allow several hoists to be physically connected together.
Compliant with AS1418 including RF spotters pendant.
Tracks
125m Jands JH Track as boundary track against the wall in each studio.
Drapes
125m of 100% fullness drapes in Studio 3 with existing drapes used in Studio 4 (recovered from Epping facility).
Power Infrastructure
3 x Vass 250A buss ducts in each studio with 50A 3-phase drop boxes for each dimmer rack – 750A capacity each room.
50A 3-phase drops on each studio wall for floor electrics and effects.
Technical Power
Single-phase RCD-protected technical power on each wall for video and audio power separate from lighting power distributed from discrete switchboard with technical earth available.
DMX Distribution
Dual universe DMX feeds to Jands DD8 splitter located in each studio, spur feeds to each run of lighting hoists and loop through system at studio floor level.
Luminaire Storage
Perimeter hanging racks for storage of excess luminaires and lighting accessories.
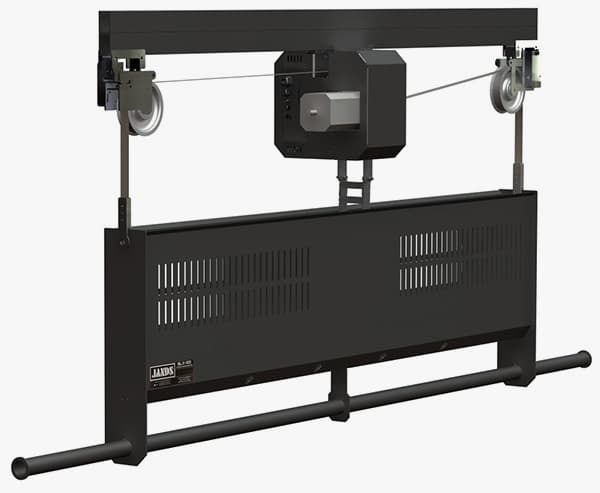
STRAIGHTFORWARD PHILOSOPHY
Within the framework of the design, the hauling equipment and battens have been tailored to meet a number of needs. Uniquely, the distribution of power, AV, and DMX/Ethernet control across the battens, catwalks, and dimmers uses localised distribution rather than centralised dimmer rooms and patching. The major benefit of this approach is the reduction of critical failure points and operational risk. An added benefit is that the placement and spacing of the battens and catwalk-mounted winch controls have been kept simple. Users can be trained without complicated induction, training, and maintenance routines. Seven believes the cost of ownership as well as ongoing training and support costs of the system will be a major benefit to the Media City site.
Mal Tennent, Seven’s Administrative Manager agrees that the straightforward rigging philosophy delivers significant operational efficiency. “They enable us to be able to speed up overnight set turnovers with the ability to link one, two or up to 25% of the battens together at any one time. The grouping function also enables us to attach 1.8m braces between two battens to provide additional lamp platforms,” he said.
Initially, Tennent was concerned that mounting the dimmers onto catwalk braces may cause noise problems. “However, the mechanical design is such that they run silently and have not caused any problems for audio,” he adds.
Of particular note was the scale and short duration of the execution phase. “There were a number of issues that could have jeopardised the outcome,” John Buckley says, “but these were identified and managed by the project team. The specification of the studios includes NR25 sound isolation on a suspended slab, super flat floors, and high-volume, low-noise air conditioning. The project builder, Watpac had good reason to be proud of the finished product as it won a Golden Trowel Award for the flatness and run-out (or lack thereof) for the studio floors. Watpac spent about five months developing and testing the award-winning process.
In essence, all agree the project has delivered both an efficient skeleton and an operational frame that is agile and capable for the future of television production. As the Seven Network told AV: “When design principles for television are reviewed, the most beneficial ones are those that deliver a system that can hold its own in a number of operational challenges. The Media City installation will stand the test of time.”
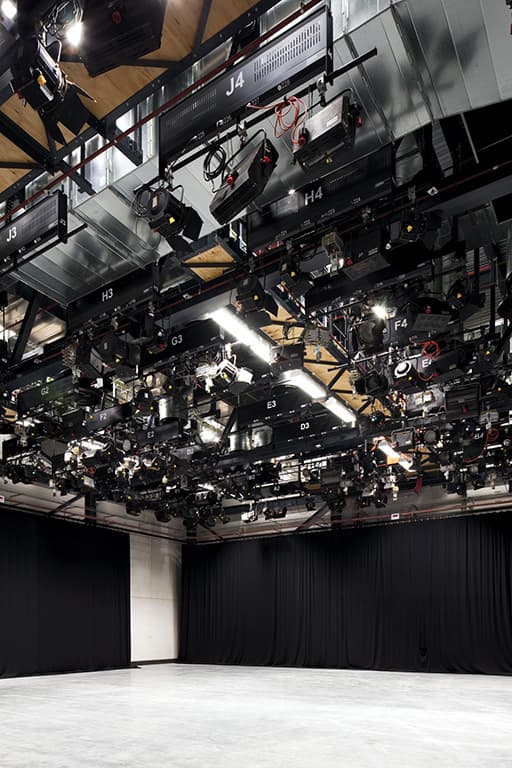
SLX100 HOIST
Lifting Speed: 12m/min (0.2m/sec)
Max Lifting Height: 8.0m
Lifting Capacity: 100kg @ 8m
Motor Type: 4 Pole AC Asynchronous
Motor Power: 0.55kW
Limit Switch: Rotary 4 pole
Safety Certification: BGV-C1
Overload Method: Cut-out switch per band
Dimensions (mm): 300(D) x 500(H) x 3000(L)
Mass: 75kg
Power Supply: 230VAC 50Hz 3A
Motor Control: Electronic inverter
Hoist Control: External switch contact with fault & limit LED reports
RESPONSES