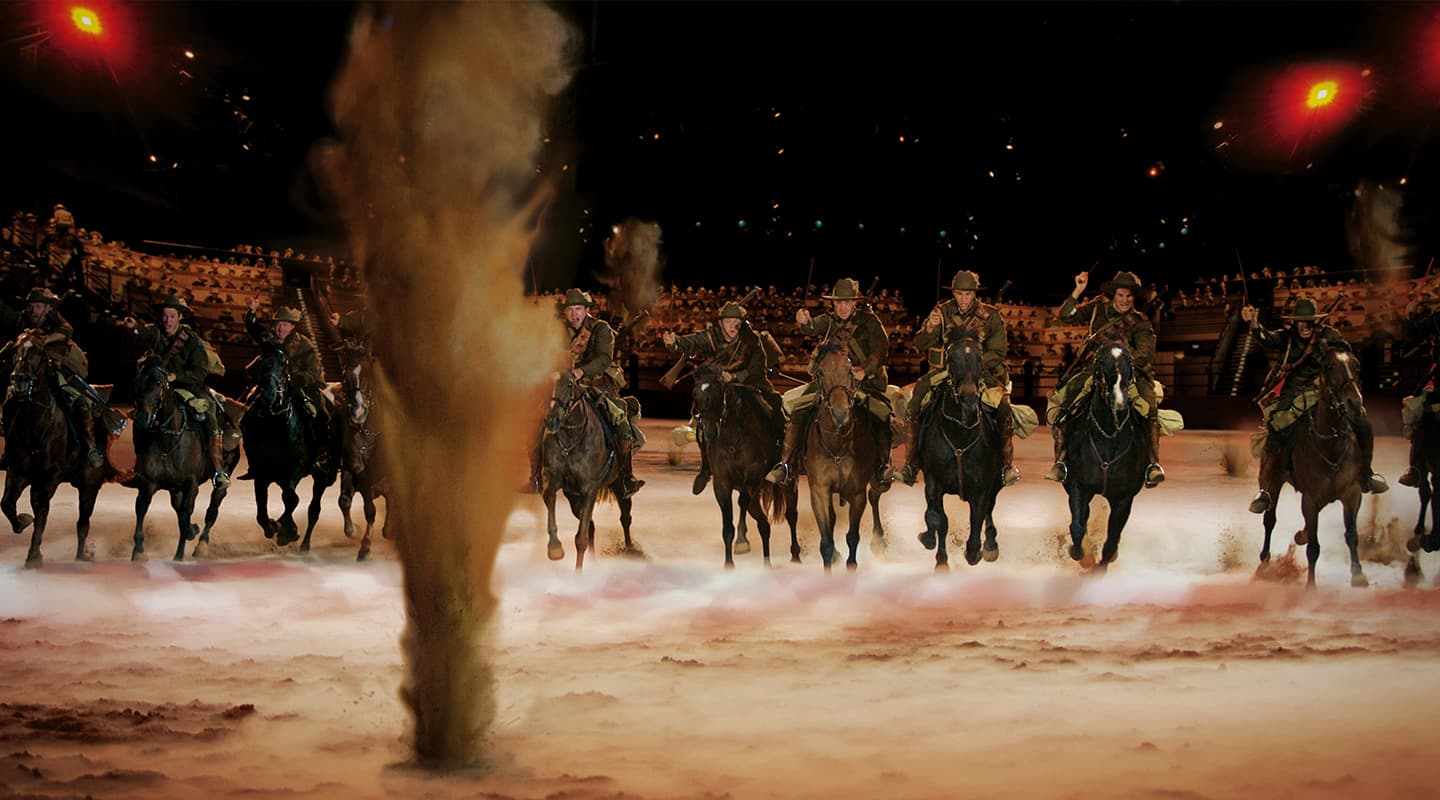
Horsing Around
Outback Spectacular 2 – Heroes of the Light Horse
Text:/ Tim Stackpool
The Australian Outback Spectacular has been the must see show on the Australian tourist circuit since its debut in April 2006, and apart from some minor changes made about a year ago, the show remained virtually unchanged until its new incarnation Heroes of the Light Horse debuted in October 2009.
Using live action, lots of horses, lots of heroes, extensive audio, video, projection and staging techniques, Outback Spectacular 2 tells the story of the legendary Australian Light Horse Brigades of World War 1, particularly the events at Beersheba in Palestine, on 31 October 1917 when the horsemen undertook a last ditch charge across open desert against around 4000 entrenched Turkish infantry.
B-I-I-I-I-G SCREEN
With a 35m-wide by 8m-high screen, the new show is all about projection. It begins with an introduction featuring amazing high definition helicopter footage of the Australian landscape. The screen continues to act as both a backdrop and a story telling medium throughout the show.
Prior to implementing the new show, the first quarter of this year was spent evaluating and selecting equipment and finalising the budgets. Rehearsals then commenced in the autumn as script and story development continued. Lighting and audio design began mid-year, while the production’s Director Simon Wincer and Producer John Menzies began shooting the screen content. Commercial realities required the existing show to maintain its five nights per week performance schedule while the new production was being developed, installed and rehearsed.
“The final piece of the puzzle – the installation of the new video projection system – happened quite late in the piece at the end of August, and then we were able to go full steam ahead with dress rehearsals and lighting and projection programming,” said Lighting Designer Clinton Dulieu. “Screen content was still being produced and edited right up until opening night.”
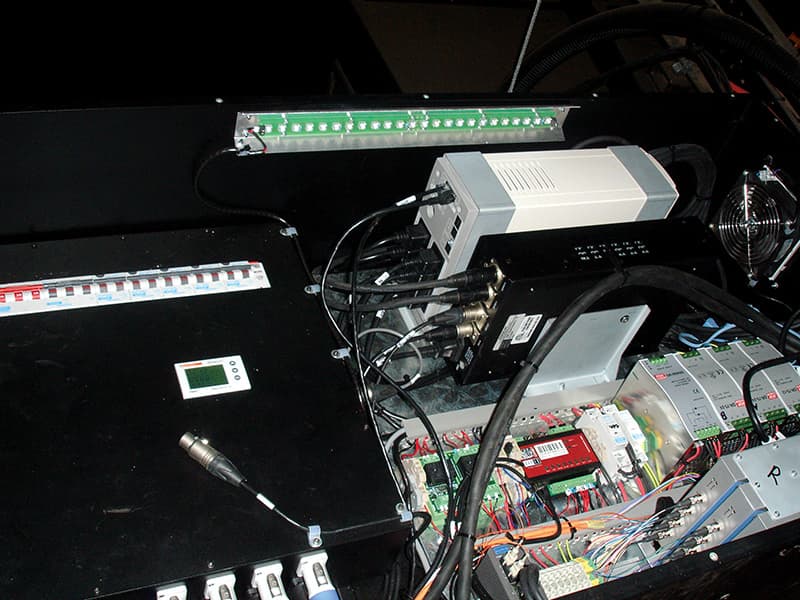
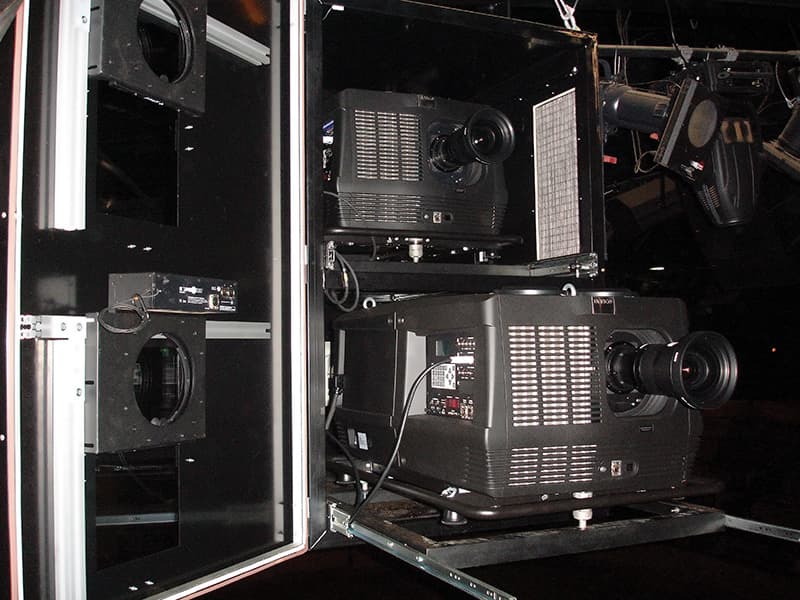
PROJECTED CHANGES
The new production required a changeover of the entire lighting control, audio front of house and projection systems, meaning the old systems needed to be operated in tandem until the new show opened. The mostly in-house production team managed the changeover by installing and working on new show components each day until around 3pm, when preparation begins for that evening’s show.
“The new Barco FLM HD20 projectors with 1.2 lenses were installed right alongside the existing PIGIs to allow us to run both during the changeover,” reports Dulieu. “Eventually I programmed the old PIGI images into the new projection system, so for the last couple of weeks of the old show we actually ran the new projectors with the old content. One of our biggest concerns was ensuring the roof could handle the additional load of the new projectors at nearly half a tonne per stack.”
The original show used a projection system based on E\T\C’s Xenon-powered PIGI scrolling film projectors which were by far the finest option available at the time of launching. “The PIGI system obviously had its drawbacks in that we could only do stills projection and the highly exposed nature of the film and projectors meant we had a lot of problems with dirt,” Dulieu told AV. “The film required constant attention and to be cleaned by hand every two weeks – a lengthy and delicate process. Obviously being film-based meant that not only were we locked in to the content that we had, and changes were expensive, but we had to replace the film entirely every nine months which too, was very expensive. When the new film first went in the images did look amazing, however the harsh environment of our venue soon took its toll.”
DISHING THE DIRT ON DIGITAL
Several years down the track, the team has embraced the improvements in digital projection, not only in terms of resolution and brightness, but also in cost. High definition projection was a particular priority for this production, as even at 3500 pixels wide, each projected pixel on a 35-metre screen is around one centimetre across. “We had pretty much narrowed down our equipment choice to video sight-unseen, then Barco arranged a full-scale demo for us on site,” Dulieu said. “It only took one look to sell management on the idea, then we set about designing the system. We went with four Barco FLM HD20 projectors which are hung in two double-stacks. One of the initial reasons for choosing the FLM over something like a Christie Roadster was that the FLM uses a completely sealed, liquid-cooled DLP engine – that’s one problem less to consider when trying to keep the dirt out.
“So we brought in Tyson Niepelt from Customised Technical Solutions (CTS) to design an environmental enclosure for the projectors. As a single FLM requires 300 litres per second of air throughput for cooling, each stack must have total of 600 litres of dust-free filtered air per second. In fact, each enclosure has eight fans, each capable of 150 litres per second of air throughput. Four fans run constantly while the other four are available as on-demand backups. That’s a total capability of just over four million litres per hour.” While the result is hardly a quiet operation, in a rig that includes 300 colour scrollers and 50 moving lights, the projector fan noise just blends with the ambient, albeit relatively high noise level.
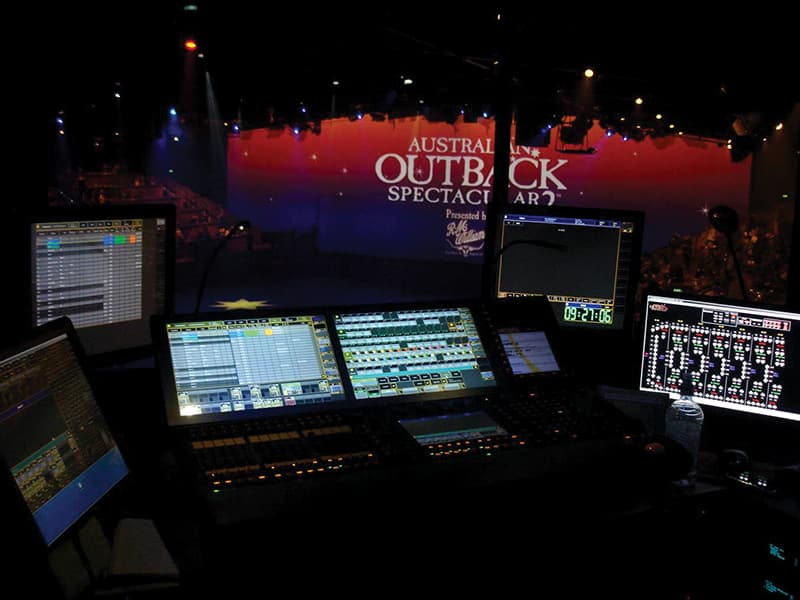
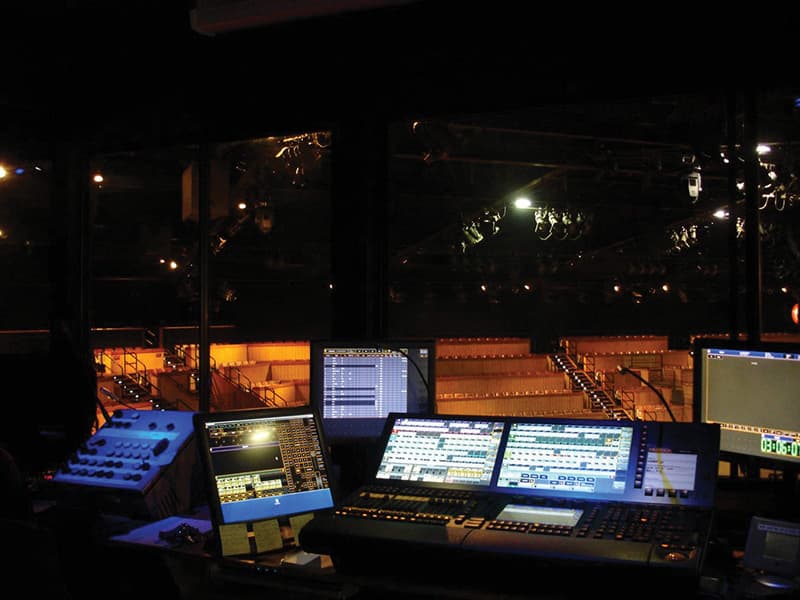
ROUTINE RUSTLING
Rigging and maintenance of equipment for the show is a major challenge. As there are no catwalks in the venue, everything has to be done from a boom lift, and the production team needs to minimise the number of occasions when the 100kg projectors are lowered down for maintenance. Inside the enclosure, each projector sits on its own cantilevered sliding drawer, secured by its standard three-point couplings. A sealed, optical-glass door on the front of the enclosure provides access to enable filters to be changed, lamps replaced and routine maintenance to be undertaken, without disturbing the line-up of the projectors. A DMX512-controlled Wybron mechanical douser is fitted to the inside of the access door to provide an absolute projection blackout when necessary.
Another custom-built enclosure sits above the cable tray adjacent to each of the projector housings. Dubbed ‘The Coffins’, these boxes contain all of the ancillary services and monitoring for the projectors and their cooling systems. Custom distribution boards built by Jands take a standard 40 Amp three-phase mains input and distribute it to the projectors and ancillary equipment. Power status is reported to a customised PLC that drives the whole box. An uninterruptible power supply provides clean power to the signal equipment and half the fans, to ensure that the projectors don’t over heat, even if in the event of a loss of mains power. A series of redundant 24 Volt power supplies feed the UPS.
Gefen converters take the optical data feed from the control booth and turn it back into DVI. Two DVI splitters then split and boost the signal to compensate for the 5m DVI runs to the projectors. The brain of the operation is a custom-coded BARIX PLC developed by CTS which monitors the power and temperature both inside and outside the projector box and drives the cooling fans accordingly. The PLC then reports the system status over the web as well as reporting back to the CTS servers in Sydney where everything is recorded and graphed. This allows for retrospective system analysis in the event of system failure. The power supply for the Wybron dousers is also in this box.
Other little touches make life easier, like LEDs that illuminate as work lights when the access hatch to the coffin is opened, and reporting when someone opens the coffin or the main door to the projectors. The system can also be setup to email or SMS whenever there is a problem, or if an unauthorised person opens the enclosure doors.
“”
Commercial realities required the existing show to maintain its five nights per week performance schedule while the new production was being developed, installed and rehearsed.
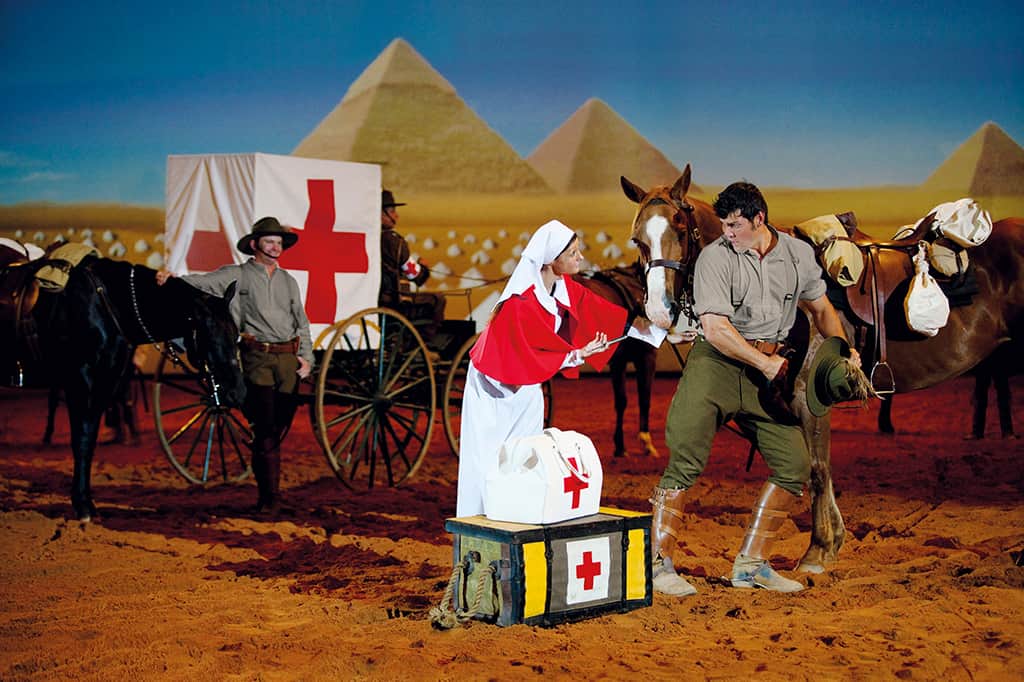
MEDIA PLAYBACK
Coolux Pandoras Box was selected as the media playback system for the production due to both the available features and the cost-effective price. Three Coolux Media Player Pros feed the projectors, one for each stack and one as a backup, a Coolux standard Media Player handles all audio playback, while a Coolux Media Manager machine ties the whole replay system together. The video replay machines are also fitted with Blackmagic capture cards fed from a Barco/Folsom Image Pro-HD to allow for the possibility of a variety of live inputs.
Back on the ground, normality prevails, with the output from each of the three Pandoras Box players being sent via DVI into a Barco 8 x 8 matrix switcher. This then feeds the six DVI-to-fibre converters and two 24-inch Samsung preview monitors. The fibre then runs to the projectors. Some spare fibre lines bring the networking info from the projectors back down via Moxa industrial fibre switches. The networking for the projectors feeds into the show network as does all other intelligent components. The PLC network goes through a VLAN and onto the corporate network, allowing access to the outside world. Strict access and firewall rules govern the traffic to ensure unauthorised traffic or other nasties don’t bring the show network down.
The Pandoras Box system is driven from SMPTE timecode as well as DMX over ArtNet. The system is quite versatile, allowing use of some of the layers on the internal timeline or triggered cues, while manipulating other layers on the fly over DMX. This combination of operating styles works extremely well, enabling the bulk of the show to be programmed on the timeline, then the brand new grandMA2 and timecode can be used to trigger the cues. At the same time, the contact closures on the grandMA2 can be used to trigger cues for projection masks to come in and out. All the output settings for each player can also be controlled over DMX, allowing the operators to easily switch the backup feed between the right and left half projector stack as required.
UNBRIDLED AMBITION
The new show is much more technologically complex than its predecessor, and that’s where much of the re-launch budget was spent. The original control ‘booth’ has been superseded with new technology, but a further change was made to the booth itself, which previously was open to the arena, along with the dust and dirt kicked-up by the performance. Early on, the decision was made to safeguard the big dollar investment made in new equipment and as such an entirely new control room was constructed. “It’s been great for us,” Dulieu said. “Keeping out the dirt, making a much cooler and more comfortable environment to work in. It’s made a big difference.”
RESPONSES