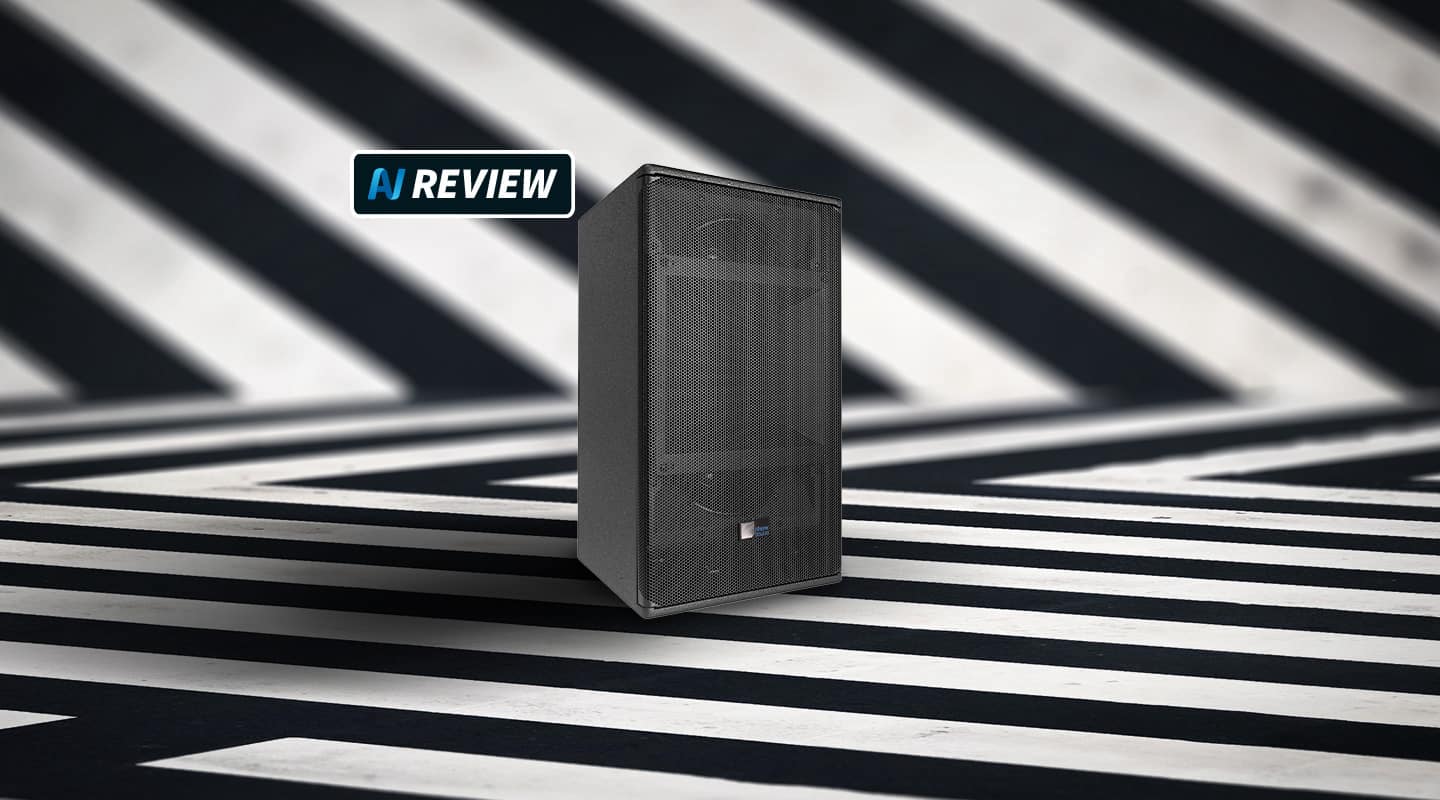
Review: Meyer Sound Ultra-X40
Meyer’s new Ultra series combines everything they’ve learnt from the UPA and LEO series into one small box. Does it do its predecessors justice? Read on...
Active Compact Loudspeaker
Meyer Sound Laboratories’ popular UPA speakers are retiring after a long and distinguished career as leaders of the professional mid-sized point-source class. The full-range passive UPA-1 was released in 1980 and was the first live speaker to use a trapezoidal cabinet – a shape that allowed for curved arrays. Output quality was maintained by a dedicated electronic controller containing active crossovers, frequency and phase correction circuits, and feedback circuits to provide driver protection. In the mid-1990s Meyer Sound embraced powered loudspeakers by putting the processing and an amplifier inside the speaker cabinet. The active UPA-1P has been delivering Meyer’s trademark high-fidelity-at-high-volume sound to appreciative audiences ever since then. Mention them around sound types and you’ll likely hear an anecdote along the lines of “I heard this big sound and it was all coming from these little speakers”. Meyer UPAs for sure…
The UPA’s replacement would have to be good, and it’s awesome. The new Meyer Sound Ultra-X40 is still a compact, vented two-way speaker but it’s a completely new design with several fundamental differences. Over the past few years of developing their LEO family of large-scale line array systems, Meyer made significant advancements in driver configuration, horn technology, low distortion and phase correction, and wanted to incorporate these in a point-source box. The timing was good to replace the ageing UPAs, and the result is a speaker that is smaller, lighter, tighter, louder and cheaper than its predecessor. Lots to like there.
UP CLOSE
The biggest difference is the driver configuration changing from the traditional horn-above-woofer two-way layout to a clever concentric-like design. The 12-inch woofer has been replaced by two eight-inch neodymium magnet drivers mounted on a concave waveguide and slanted inwards. Mounted between them is the central rotatable waveguide for the three-inch high-frequency compression driver. Applying some array trickery to the eight-inch drivers and coupling them with the back of the horn waveguide delivers a coaxial point source experience with exceptional directional control. Dispersion for the Ultra-X40 is a wide but focused 110 x 50 degrees (the Ultra-X42 variation is 70 x 50 degrees) and that pattern is maintained down to a low 400Hz.
The two eight-inch drivers have a collective cone area similar to a single 12-inch driver but they’re narrower and the horn is in between them so the Ultra-X40 is not only smaller but is also about 9kg lighter than its direct predecessor, the UPA-1P. That’s a significant difference and broadens its potential applications – although there is no facility for using it as a floor monitor. It can fit into a smaller case, and it’s small enough and light enough for one person of reasonable strength to put it onto a stand.
Meyer noticed users were making their own mounting brackets for the UPAs, but they shouldn’t need to with the comprehensive range of custom-made accessories for the Ultra-X40. The speakers are fitted with 11 x M8 threaded points, and options include a hanging yoke, u-brackets, cluster plates for locking speakers together, plus the pole mount. For horizontal mounting the horn can easily be rotated via four screws under the grille; it doesn’t need to be removed from the cabinet.
The cabinet is made from multi-ply birch and the overall look is professional but understated. The textured finish looks like the finish on other speakers, as does the perforated grille, but the angled speakers and big horn behind the grille look purposeful and modern. There are no side or top handles, resulting in a clean look. The chunky handles on the back are good for general handling and protecting the connecting leads, but they’re not much help if you’re lifting it onto a stand.
CONNECTIONS
The rear of the cabinet is mainly heatsink with a powerCON20 in and out. Connections are professionally minimal – an XLR in and out is all you get, with LEDs indicating power, signal and limiting. This is fine for large-scale productions and installations but for smaller shows a volume knob can be handy; I had one show where the speakers were linked together and I wanted to run them at different levels due to their placement. The only time I missed a power switch was powering down at the end of a long night when it seemed a lot to go around to the back of the speaker to unplug the power lead.
The connection panel is modular and may evolve over time. At the moment an optional five-pin XLR version is available that will connect audio plus the RMS remote monitoring system for remote muting or providing a readout of the loudspeaker parameters via Meyer’s ‘Compass’ software. Meyer are one of the manufacturers behind the emerging Milan network protocol that seeks to combine the AVB standard with defined device requirements so the machines can talk to each other. The results of that could lead to a networked version.
Inside the cabinet, Meyer’s ‘Intelligent AC’ automatically selects the operating voltage and conditions the power by controlling voltage peaks and interference, while their proprietary audio chain does its thing with the phase and frequency response – resulting in the flat response, coherence and impulse response that gives these speakers their special sound.
Meyer make all their drivers in-house to ensure complete quality control and maximum integration between components. Power to the drivers comes from a new power-efficient, air-cooled, three-channel Class D amplifier capable of 1950kW peak. Cabinet size may be down but volume is up – the stated linear peak SPL of over 130dB [measured free-field at 1m using Meyer’s M Noise] from a speaker weighing less than 24kg is class-leading.
NEED TO KNOW
PRICE
$9,999 RRP
CONTACT
Meyer Sound: meyersound.com
PROS
Point source fidelity
Controlled dispersion
High power-to-weight ratio
Handy size
CONS
No volume control
Limited I/O
SUMMARY
Meyer’s new Ultra-X40 is the result of decades of on-going research and improvement in the pursuit of technical excellence, offering a tightly-controlled dispersion and high quality sound in a box that is surprisingly smaller than it sounds.
IN USE
The Ultra-X40s proved to be a delight to use and a crowd-pleaser. The first time I used them was at my usual testing ground, the Theatre Royal Castlemaine. We’re already fans of the brand; the house PA is a double Meyer MSL-3 system (plus four 18-inch subs per side) and works well in the 400 capacity room. In some ways the similarly shaped Ultra-X40s are a modern, considerably shrunken version of the 40 year-old MSL-3s. The specs are almost the same in terms of frequency response and volume (and also in terms of coverage if compared with the narrow-throw Ultra-X42 variation). As an indication of progress made over the last decades, the Ultra-X40 weighs 24kg while the MSL-3 weighs 110kg each… plus amps.
I often set up extra speakers for a front in-fill at the Theatre; sometimes to fill the hole, sometimes for testing purposes. The X40s are an ideal size for my in-fill, but my first impression was how easily they could fill the whole room and compete with the main system. The big PA had more woof and rumble, but the X40’s mid-range was clear and coherent at the back of the room. They worked well together and the big system sounded a bit hollow without the X40s. The band that night was Finder Lover Seeker, an act that needed the three female vocals to be heard clearly above the full band sound. Their mixer, Sarah Madigan, had fun and at the end said she thought most of the vocals were coming from the X40s.
The next week the Theatre Royal hosted Paul Kelly performing with Alice Keath as part of his recent ‘Love Is Strong As Death’ tour. I was doing sound for the Victorian leg of the tour, and had a similar experience to Sarah at the front of house. Using the X40s as in-fill changed the sound in the room; they didn’t seem to interfere destructively with the main system, but added real midrange clarity. They don’t mind going loud (their level needed to be watched to avoid interfering with the stage monitors), but the quality invites you to turn them up and it’s like opening the throttle on a powerful car – they lift up and go. Best in-fills I’ve used by a good margin.
A big reverberant old church in Maldon, as part of the Maldon Folk Festival, was too easy for the Ultra-X40s. I used them instead of a stack of black boxes and won’t be going back; the point source delivery and controlled pattern cut a slice of clear sound through the potentially boomy, washy room. The condenser mics were beautifully detailed on the fine instruments and stayed stable when turned up to working level. An audiophile’s treat, they have the ability to draw your ear back through the speaker to the source. Every touch of EQ, effects or panning is clear. This transparency is a Meyer Sound trademark and, along with their ability to faithfully reproduce all styles of music, is the reason for their reputation as exceptional speakers for theatrical applications.
The annual Mountaingrass Festival was tougher. A new location for the main concerts had around 300 people sitting in an odd-shaped, half-dead, fluttery conference room. It’s a Bluegrass festival and opening up the condenser mic centre stage is always a good test – and one that this room largely failed. Unfortunate dimensions and fittings meant it was not going to give any real volume before it wanted to feed back. We had a good modular black box system that usually does the job (previously in a big marquee) and a pair of Ultra-X40s. We set them both up and, as well as a noticeable difference in audio quality, the X40s were much smoother off-axis and more resistant to feedback. I tried pointing the two systems in different directions but that didn’t last long; it was sort of louder and covered a bit wider, but the modular black box system was interfering and detracting from the quality of the X40s – so I turned the modular speakers off and ran the X40s all weekend. The room needed a couple of ugly EQ cuts, but after that the X40s provided a fuller sound than you’d expect from a pair of speakers on stands in a big, bad space. The bass doesn’t sit loud in the mix for this music but it has to be there, and those upright basses go low; I was pleasantly surprised at the depth and clarity with no sense of strain. Bluegrass bands have a low average volume but extreme dynamics, and the mics are wide open. When they hit hard the meters jump and that’s another good test for a system; many get harsh in this situation, but the Ultra X40s revelled in the peaks. The audience at these acoustic events are very aware of sound quality, and I was getting the right reaction from them – along with some surprise that it was all coming from the little speakers. It’s that UPA thing all over again.
Back in the real world, the final test was loud bands with the Ultra-X40s and separate subs. I was already impressed by what a pair of X40s could do on their own, but bands always need more. A Christmas party at Lot19, an artist colony and centre of Castlemaine’s alternate culture, was the test I wanted: an outdoors gig with two bands and DJs. The headline act was Vibrasonics, a 10-piece funky dance band using 24 channels to FOH and six foldback sends. I’ve used and reviewed a lot of mid-sized powered speakers, waiting to find one to replace my comparatively lo-fi but tough and loud double four-way black box PA. The X40s combined with subs are the first to do it, the subs need to be good to keep up with them (Meyer recommend their LFC-750 subs). With a big bottom end under them they handled the whole band easily and also proved exceptionally good for music playback, similar to studio monitors in their detail and the way they draw the ear to subtleties in the original recordings. The DJs were happy and at the end of the night, packing up on stage with the tunes still cranking, it was noticeable how quiet and nice the X40s sounded from behind. Great vibe and the speakers were part of it; I pulled the pin at 2:30am under some protest.
CONCLUSION
The Ultra-X40 is a genuine general-purpose speaker that will get used in theatres, theme-parks and stadiums on its own or as part of bigger systems. You could put it anywhere thanks to its combination of low width and the rotatable horn; it’s ideal for under balconies or filling holes. The size and weight makes it more suitable for portable use than the heavier UPAs, and although it’s expensive the sound quality justifies the price. Along with the sound quality, the Ultra-X40’s practicality and expected long-term reliability may prove attractive for small operators as well as hire/installation companies.
The Ultra-X40 is the product of continual improvement in the pursuit of technical excellence, and will prove to be a worthy successor to the venerable UPA series. Meyer Sound have long been proponents of self-powered speakers, citing simplicity, increased fidelity and controlled integration between amp and drivers. They knew they had a hit on their hands when they took record numbers of pre-orders from trade shows on release. The Ultra-X40’s point source design offers superior sound quality, its tight dispersion gives predictable results, and its lighter and smaller enclosures increases practicality and placement options. State of the art.
ULTRA OPTIMISED
Mark Woods talks with Pablo Espinosa, Meyer Sound’s Vice President & Chief Loudspeaker Designer, about the Ultra-X40.
Mark Woods: How do the Ultra-X40s maintain their dispersion pattern below the horn’s crossover frequency? Is there some kind of array behaviour with the eight-inch speakers? Or is it the wave guide they’re mounted on?
Pablo Espinosa: All of the above, and more. When using a single driver, the polar pattern of the driver is dominated by the size of the driver and the frequency being reproduced – this is just physics. One of the huge advantages of using two drivers in this configuration is that the combined polar pattern of the two drivers can be controlled and optimised to well below their crossover frequency. In addition, the polar pattern can also be optimised to interact with the horn’s polar pattern to create an incredible smooth transition at crossover, on-axis and off-axis.
MW: How did the R&D from the LEO range contribute to the Ultra-X40?
PE: We started with this driver configuration and horn technology 10 years ago, and took it to the next level with the LEO family. As the family grew, every new member brought innovations. All these innovations contributed to the Ultra-X40.
To create a product like the X40, it’s not just a matter of ensuring that each individual part (drivers, enclosure, horn, amplifier, etc.) has ‘best-in-class’ performance. They all have to be optimised so that each part interacts perfectly with all of the others to create a result that goes above and beyond putting a bunch of OEM components together. That understanding and optimisation process is the most important contribution from the LEO family.
RESPONSES