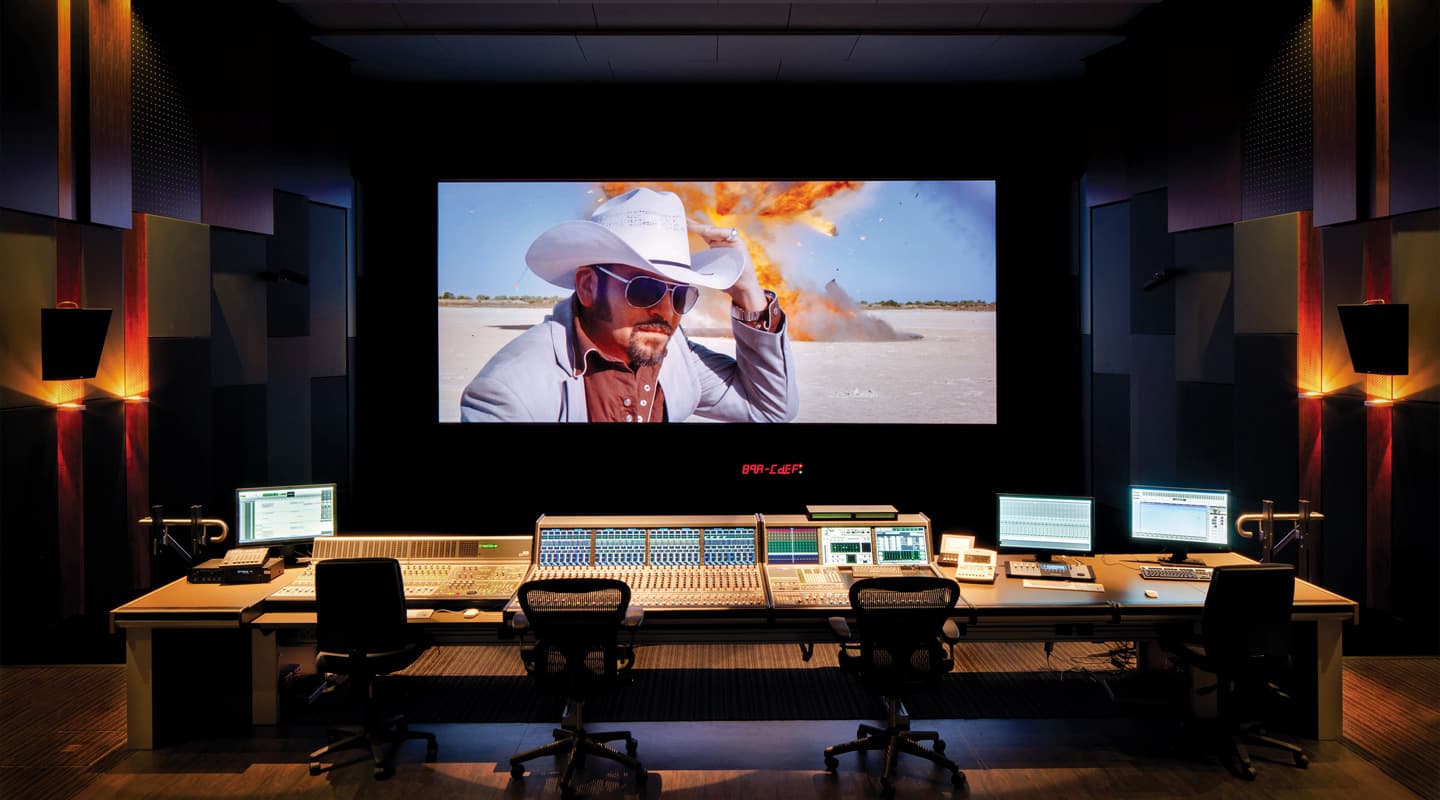
Creating a Premier Project
SA Film Corporation’s new Adelaide Studios.
Text:/ Derek Powell
Images:/ Courtesy of the SAFC
Photography by Peter Barnes
Recently, the Adelaide Studios, new home of the South Australian Film Corporation (SAFC), opened for business. The entire project won plaudits and awards, but for the team involved in the creation of the mixing studios, there was one particularly satisfying moment.
The film mixing studio was designed to meet the demanding Dolby Premier Studio Certification standards and the team won the coveted accreditation in a slam-dunk at their first attempt.
FIRST TIME FIRST TRY
The Dolby representative was stunned, conceding that this was the first time any facility had passed the ultra-stringent test and measurement regime at the first visit. As a rule, there’ll be a list (and sometimes a very long list) of acoustic and electronic improvements to be made (and a return visit by the accreditor) before the rare and highly prized certificate can be hung on the wall. Not this time. While it surprised the man from Dolby, for two members of the engineering team, this was simply the culmination of a thirty-year journey to bring a world-class feature film mixing facility to the SAFC.
Both acoustical consultant Dr. Peter Swift (from international technical consultancy AECOM) and studio consultant Mike Rowan have been involved with the SAFC since much humbler times. The first SAFC mixing studio, featuring a 12 channel Quad-8 console and Magna-Tech sprocketed-tape dubbers was created by walling-off the dress circle of a disused suburban cinema. Rowan noted that while it was put to good use on documentary and television projects, it wasn’t in the class of the next iteration, when in 1980, the corporation moved to a former munitions factory in the outer Adelaide suburb of Hendon.
QUIET BEGINNINGS
There, Rowan created the first true film mixing console, accommodating three operators at once, who took care of dialogue, music and effects. As the years passed and projects became more ambitious, Peter Swift was called in from time to time to improve the acoustics. Meanwhile Rowan supervised the upgrade of the console to a Harrison Series 12 with the faithful Magna-Techs supplanted by synchronized Tascam DA-88 eight-track digital tape transports.
Finally, after 30 years in Hendon, the SAFC and the studios have been given a new home as part of the redevelopment of the historic Glenside Hospital site, a former mental health facility. Along with the Dolby Premier studio, the magnificent new Adelaide Studios facility comprises two sound stages, a full suite of production offices, ADR/Foley studios, and 96-seat screening theatre.
I spoke with Architect Steve Grieve, who led the design team, about the constraints of working on the heritage-listed Glenside Hospital site. “We decided early on that to tailor the original building to come up to spec would compromise their heritage value,” he told me. “Our intervention in the building to get it to perform acoustically would have pushed the limits on what’s acceptable. So we decided to put all the technical facilities in a new building”.
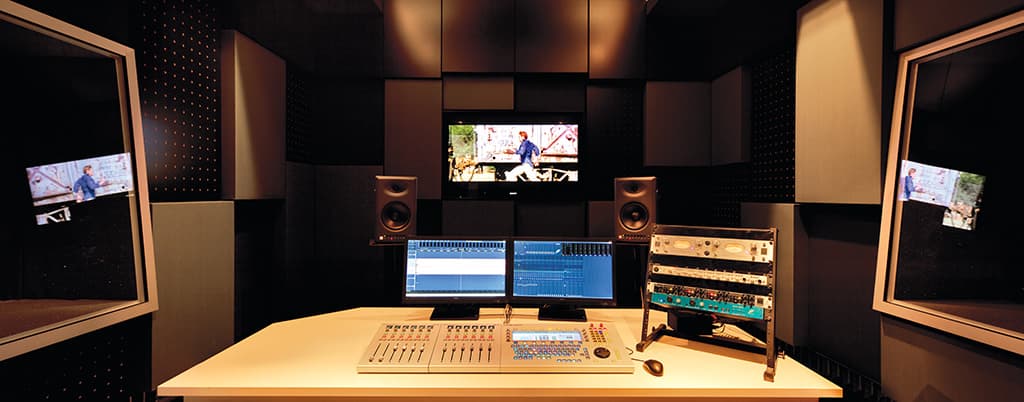
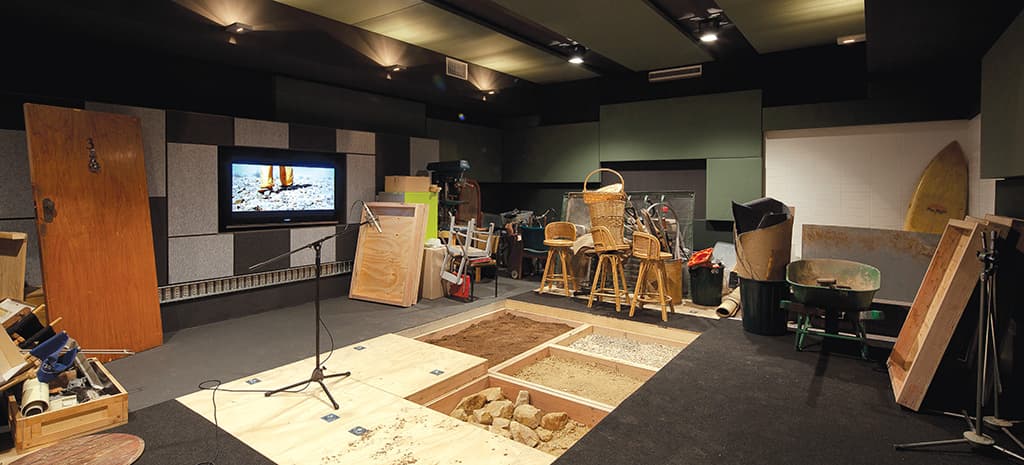
DOING IT ON THE QUIET
After previous incarnations in adapted and refurbished spaces, the new build provided the opportunity for the architectural and acoustical team to finally apply a rigorous approach to two vital objectives for the Premier theatre – keeping out extraneous noise and building-in perfectly-tailored acoustics.
Very low levels of external noise in the studio are crucial to the Dolby Premier specification, so SAFC engaged Swift to assess the level of noise from aircraft, passing trains and ground-borne vibrations at a number of potential sites before Glenside was chosen. However, from a noise point of view, a quiet location is just the start.
Peter Swift explained that the mixing studio itself is essentially a separate structure within the studio building. “…there are actually structural breaks all around,” he noted. “So where services cross, there are flexible connections”. Making certain of the structural separation was a key challenge, as he described. “Whenever the slabs were poured, with the appropriate isolating material between them, you’ve got to make sure that pieces don’t fall down the cracks and cause little transmission bridges. Because once you start building walls up inside – if you haven’t found them, then it’s too late. You’ll never find them.”
‘Hold points’ were built into the construction schedule to allow the AECOM team to measure the relative vibration levels between the isolated slabs to make sure nothing was amiss. It was exacting work, but the pay-off was extremely low levels of airborne and structure-borne noise in the mixing theatre.
THEN KEEPING IT HUSH HUSH
Designing the frequency response of the space was a step-by-step process, relying heavily on physics and mathematics, but also on some simple geometry, Swift explained – launching into what was virtually a master-class in studio acoustics. The first stage, once the volume and the basic proportions of the theatre were established by the Architect, was for Swift to use the raw dimensions to calculate the ‘modes’ or standing-wave frequencies that would exist in the space. He then set to smoothing out the potential resonances by tweaking the dimensions of the walls slightly and running all the calculations again until he had the proper distribution of modes across the audio spectrum.
Next, using some simple ray-tracing diagrams, he adjusted the angles of the walls, ensuring that the first reflections from each speaker would be directed away from the mixing position. “Any reflections that you do get need to be a little bit late and at least 10 and preferably 20 dB down which means you’ve got to really look at the relationship of the side walls and the absorption on them,” Swift pointed out.
From there, a key part of the process is designing the right mix of absorption in each frequency band to meet the crucial reverb time versus frequency parameters. “You can’t just put soft, wide-band absorption across the whole theatre – it gets too one-sided, so you’ve got to mix wide-band and low frequency with a bit of reflective stuff”, he said.
There’s heaps of maths involved so that the right absorption gets installed, but at the end of the build Swift still allowed for time to do the crucial final measurement and tuning of the absorbers by hand.
“”
this was simply the culmination of a thirty-year journey to bring a world-class feature film mixing facility to the SAFC
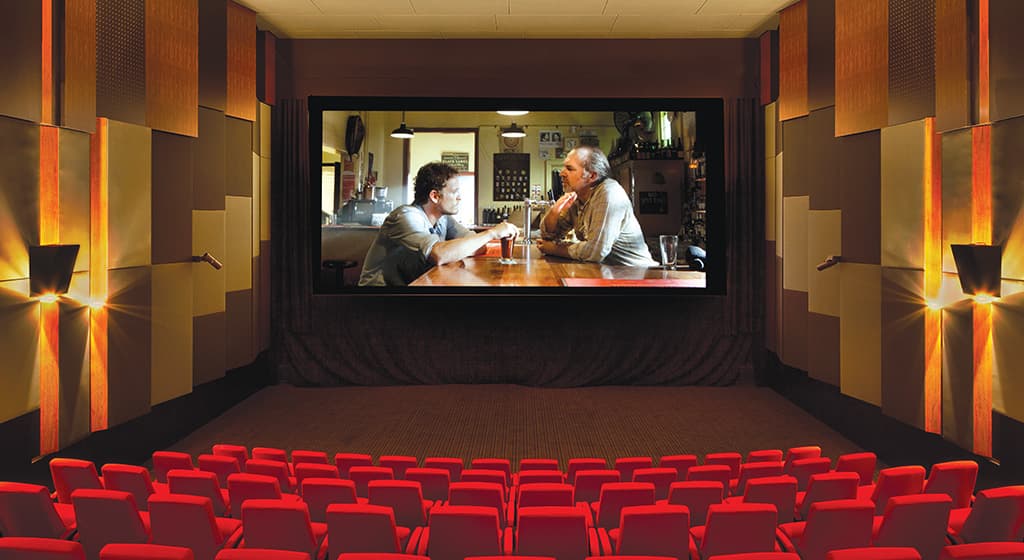
STRUCTURALLY SOUND
The architects worked closely with Swift, adjusting their structural design to each iteration of his calculations. I asked architect Steve Grieve if he found the process unduly constraining. “Not at all”, he replied. “If you understand the Dolby specifications well enough from the point of view of performance requirements, then you can work with the acoustic engineers to develop the identity of the space itself. In the case of the screening theatre and the mixing theatres in particular – often the absorption panels have a particular pattern and texture. The actual materials have to be exposed so they work acoustically, so if you work with them, you can use them as a design feature.” The end result, highlighted by well-placed lighting, is simply stunning and the theatre looks every bit as spectacular as it sounds.
Meanwhile, working with AECOM AV consultant Mike Comiskey, Mike Rowan set about assembling the equipment side of the equation. For speakers, Rowan turned to their established supplier Krix, whose SA-manufactured and THX-certified cinema speakers are exported around the world. He settled on three identical KX-5920 3-way boxes from their commercial cinema range for left, centre and right, with each driver powered by one QSC 3422 or QSC 1644 amplifier channel. Subs were a pair of massive twin-18inch KX-4610s, while 12 KX-1870 two-way boxes, each driven by a QSC 1622 channel, took care of surround. To minimize losses across the speaker cables, the QSC amps driving the front speakers were located adjacent to the enclosures, behind the micro-perforated screen.
An upgrade to the existing Harrison console was next on the agenda. Rowan chose the Harrison MPC4-D console, optionally working in concert with a ProTools D-Command 16-channel control surface. The Harrison console is attractive because it is in wide use for film, enabling interstate and overseas mixers to familiarise themselves with the room easily. For different projects, a sound engineer may to elect to mix from the Harrison console or from the ProTools interface. This would be an issue in most facilities as only one control surface could be positioned in the “sweet spot” at the centre of the room. However Mike Rowan devised an ingenious solution that allows the console to be reconfigured in less than ten minutes, so that either the ProTools or the Harrison can assume “centre stage”. He built an extended metal framework that spans the full width of the combined consoles. When required, the ProTools surface can be lifted out, then using a system of slides, the Harrison left console can simply move across making space for the ProTools to be placed in the centre
As befits a team with such impeccable local credentials (and the patience to spend 30 years perfecting their ideas), the Premier Studio is an absolute triumph. It looks spectacular, operates immaculately and has now been certified by Dolby as sounding absolutely flawless.
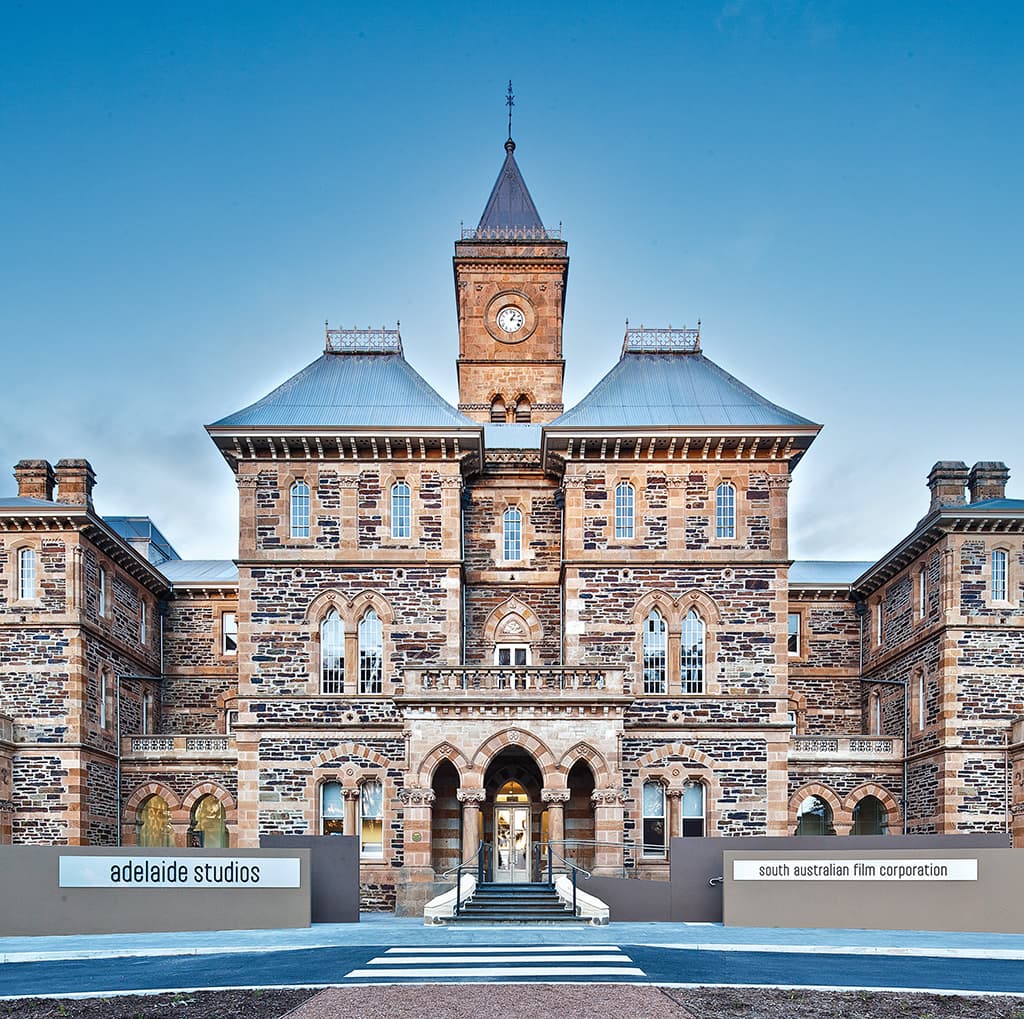
PROJECT TEAM
Architects: Steve Grieve – Grieve Gillett (SA) in association with
Joe Agius – Cox Richardson Architects and Planners (Sydney).
Consultants: Dr Peter Swift (AECOM) acoustic engineer
Mike Comiskey (AECOM) audiovisual consultant
Mike Rowan Studio Consultant
Web References:
Adelaide Studios: www.adelaidestudios.com.au
Dolby Premier Certification: www.dolby.com/gb/en/professional/service/cinema/dolby-premier-studio-certification.html
A brief history of the Glenside Site prior to construction: www.abc.net.au/local/photos/2011/05/11/3213910.htm
EQUIPMENT LIST
MIXING THEATRE
Harrison MPC4-D console
Harrison X-Range digital engines
ProTools D-Command 16 channel console
CB Electronics SR24 synchroniser/controller
CB Electronics timecode/footage display below screen
Rosendahl NanosyncsHD DDS audio clock and video sync generator
NEC NC1200 (9300 lm) 2K projector
SCREENING THEATRE
NEC NC3200S (33,000 lm) 2K projector
Kinoton FP 30 E 35mm film projector with digitally-controlled sprocket drive
BOTH THEATRES (per room)
Harkness Perlux 140 MP screen and masking
Theatre Supplies ports
Dolby CP650 digital cinema sound processor
QSC DCM 30D amplifier controller
QSC DCA 1622 amps to surrounds
QSC DCA 3422 amps to L, C & R low
QSC DCA 1644 amps to L, C & R high & mid
QSC DCA 2422 amps to L & R subwoofers
Krix Speakers
3 x KX-5920 L, C, R
2 x KX-4610 subwoofers
12 x KX-1870 surround
RESPONSES