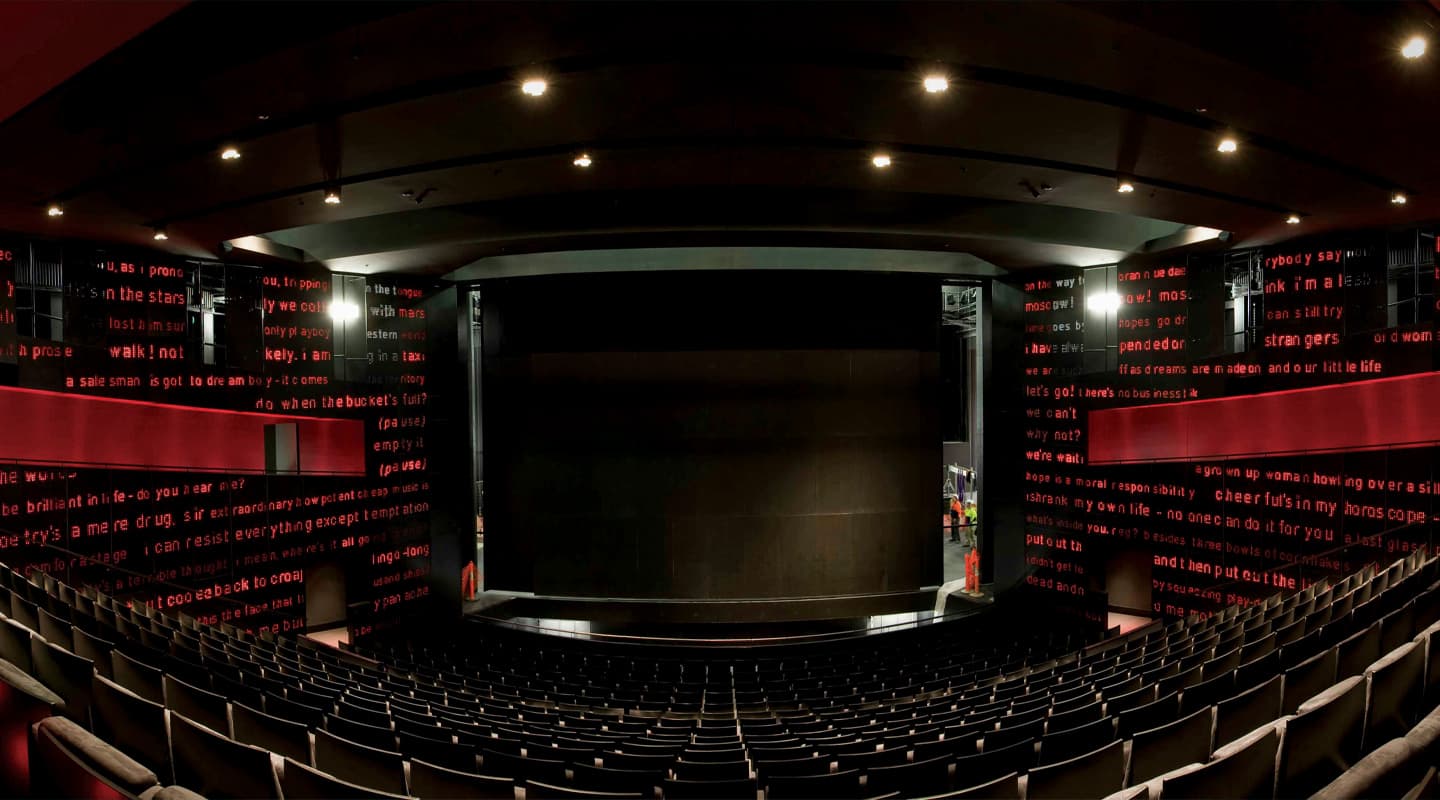
Theatre of (Your) Dreams
At last, a theatre that’s thought of everything.
Text:/ Andy Ciddor
When you’ve been staging productions for over 50 years, you can’t help but have a few ideas about how your shows should go together and what facilities can make the shows easier to stage and run. Decades ago, before they left their erstwhile home in Russell Street for their long sojourn in Melbourne’s Arts Centre, the production department at the Melbourne Theatre Company (MTC) began making notes about what their future theatre might be. Over the years ‘The Brief’ as it became known, gradually accumulated the company’s ideas, aspirations and dreams for what would one day become their permanent home theatre. Along the way there were at least nine proposals for a new MTC theatre at various times and various locations, and although on each occasion the project eventually fell through, the experience gained in working on these proposals was also absorbed into ‘The Brief’.
When in 1999 architects Ashton Raggat McDougall won the competition to design the MTC/Melbourne Recital Centre project, The Brief was provided as an attachment to their contract and became the de facto ‘user manual’ for the project. It was duly handed on to the project’s theatre and acoustic consultants Arup which entrusted it to their theatre consultant, the late Denis Irving, as the starting point for the theatre’s technical specification. During construction it also became the primary reference document for the builder Bovis Lend Lease and Jands as the Theatre Engineering Contractor.
Recognising that this would be their only opportunity for a very long time to get a new theatre of their own, in 2004 MTC appointed a Theatre Development Manager, Craig Gamble, to represent them directly at all points in the consultation, planning and construction processes. His role was to ensure not only that their brief was adhered to, but that all decisions about the construction, equipping and operational capabilities of their new theatres took full account of the end user’s needs and point of view.
In February 2009 the fruits of this planning, consulting design and construction process opened its doors to the public.
The main venue, the Sumner Theatre, is a beautiful 500–560-seat performing space that, despite its size, feels and sounds surprisingly intimate, while the 160-seat Lawler Studio is a very well conceived black box studio space (although it’s actually deep maroon with adjustable black curtains).
LESSONS LEARNED
The lessons learned from years of working in such less-than-ideal venues as MTC’s former homes at Russell Street, St Martins Theatre and the Athenaeum theatre, were incorporated into the brief to make these venues the best working theatres that could jointly be imagined.
The loading dock is directly connected to both stage areas, and at the same level. There is a stage management/props kitchen for preparation of stage food. There are storage and show maintenance areas for all departments. It’s possible for performers to get from backstage to auditorium entrances without going out into the street or parading through the foyers. There is a goods lift that offers direct access to every level of the stage house from the sub-stage to the winch room. The stage management/prompt corner system can operate from either side of the stage, the control room or the production desk position in the house. Performance technical staff can get from backstage areas to the control rooms, spot positions and other working points without battling foyer crowds or climbing through blacked-out roof spaces. Through the use of Jands hand winches, the house lights can be maintained and re-lamped without ladders, scaffolds, bosun’s chairs, licensed riggers or trained acrobats. There are configurable and extendable work light (white) and running light (blue) systems throughout the venues. Are you getting the picture?
As you’d expect, both venues are well equipped with high quality equipment, as befits a flagship theatre company.
The Sumner’s main stage area of approximately 26m wide x 19m deep (including 6m rear stage area) with a scenery flying height of 20m, is as capable a space as anything found anywhere in the world. A Stage Technologies Nomad system, controls some 64 motorised 500kg fly lines, coil-spring lighting cable-reelers and half a dozen ASM 250kg band hoists for spot lines. The Yamaha DM1000 audio console, feeding theatre sector’s favourite Meyer speakers – configured for stage sounds and sound effects – will serve as a solid base for whatever productions come along. The 4000-channel ETC Eos console will certainly take good care of the 460 IES dimmers, driving just under 500 conventional fixtures and 16 moving lights. The large number and wide selection of Selecon, ETC, Martin and Quartzcolour luminaires will never be enough for any lighting designer; but neither would twice as many. Similarly, there is a good stock of stage drapery, but every production will still require a skip full of black tatt to finish off the masking. This venue is as well equipped as drama gets, and then a little bit more, but that’s not why this is an amazing place for making theatre.
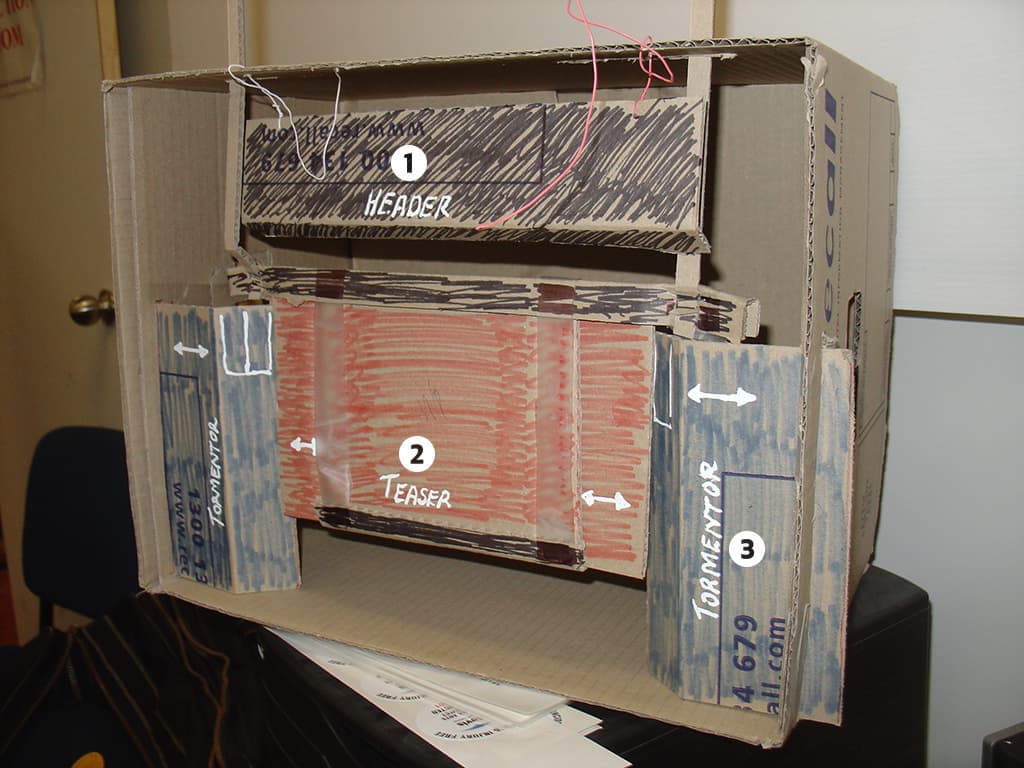
Left: Not only was stage terminology and technology initially unfamiliar to the team from project builder Bovis Lend Lease, but the concept of the re-sizeable proscenium opening (that could move in so many directions at once) was hard to pick up from the engineering drawings. To make the concepts abundantly clear, the builders knocked up this down ‘n’ dirty, not-even-slighty-to-scale, model.

Right: A view from the stage showing what the cardboard model was actually describing: (1) The proscenium header; (2) The teaser; (3) The tormentor with its panels and Juliet balcony.
CURTAINS!
One of the more unusual features of the Sumner Theatre is the absence of that long-standing public health institution: the fire curtain. Provided as a safety measure to protect the audience to be from the once-fairly-regular conflagrations that would break out on stage, the concept was that this non-combustible fire curtain would be lowered in to trap the fire on stage, immolating the performers and crew, while the gentlefolk in the audience had time to flee from the auditorium.
To meet their onerous fire ratings, most fire curtains are constructed from a framework of steel beams covered with a non-combustible material such as metal, fibro-cement sheeting or even asbestos sheeting. Weighing several tonnes and occupying a slot some 150mm–300mm deep in the proscenium arch, these fire curtains are required to completely seal the gap between the stage and the auditorium. No scenery or props are permitted in the path of the fire curtain, and any mechanism to allow for adjustments to the proscenium opening must still maintain the critical fire seal.
Theatre consultant Dennis Irving sat down with the fire authorities in Melbourne and persuaded them to rethink the problem of audience safety. As the purpose of a fire curtain is to allow the audience to exit safely in the case of a fire, Irving proposed that by providing enough clear exit paths from the theatre, and using a stage ventilation system that prevents the smoke from a stage fire from entering the auditorium, there would be sufficient time for an audience to get safely out of the building without the need for a fire curtain.
By accepting Irving’s proposal, the fire authorities cleared the way for the design of a reconfigurable proscenium frame and freed set designers from having to leave a hole in their sets to accommodate the lowering of the fire curtain. Thus, unlike any other major theatre in the country, through some smart design by MTC and clever engineering by primary contractor Jands and Steve Conroy at ShowTrek Productions, the Sumner’s proscenium opening, complete with Juliet balconies, is variable in width from 11m to 16m, and also variable in height from 0m to 9m, while always looking like an architecturally-solid wall.
“”
In place of a matrix of tens of thousands of LEDs, the words were created by drilling patterns of holes in sheets of 32mm plywood
LIGHTING EQUIPMENT LIST
Lighting Console
- ETC Eos 4000
Dimming
- 756 outlets via ETC/IES Matrix dimming system to 460 dimmers
- 372 x 2.5kVA phase controlled dimmers
- 36 x 5kVA phase controlled dimmers
- 42 x 10A non dimmed (relays)
- 6 x 20A non dimmed (relays)
Profile Spots
- 4 x ETC Source 4 5° (750W)
- 20 x ETC Source 4 10° (750W)
- 60 x ETC Source 4 19° (750W)
- 60 x ETC Source 4 26° (750W)
- 50 x ETC Source 4 36° (750W)
- 20 x ETC Source 4 50° (750W)
- 8 x Selecon Pacific Zoom 45 – 75° (1000W)
- 20 x Selecon Pacific Zoom 23 – 50° (1000W)
- 20 x Selecon Pacific Zoom 14 – 35° (1000W)
Fresnel & PC Spots
- 40 x Selecon 250mm lens Fresnel (2000W)
- 30 x Selecon 175mm lens Fresnel (1200W)
- 30 x Selecon Rama 175mm PC spot (1200W)
- 20 x Selecon Acclaim Fresnel (650W)
Cyclorama
- 12 x Quartzcolour Iris 4 cyc floods
- 12 x Quartzcolour 4 compartment ground rows
Beamlights
- 80 x ETC Source 4 Pars each with a full set of lenses and reflectors (750W)
Moving Head luminaires
- 8 x ETC Revolution with shutters (750W)
- 8 x Martin TW1 wash (1200W)
Follow Spots
- 2 x Robert Juliat Super Korrigan HMI (1200W)
Atmospheric Effects
- 2 x Look Solutions Unique hazers
- 2 x Rosco 1700 smoke machines
Accessories
- 8 x Boom bases
- 6 x Boom trolleys
- 80 x Boom Arms
Lighting Bars
- 20 x Jands JLX wired lighting bars fed via Conductix-Wampfler cable reelers
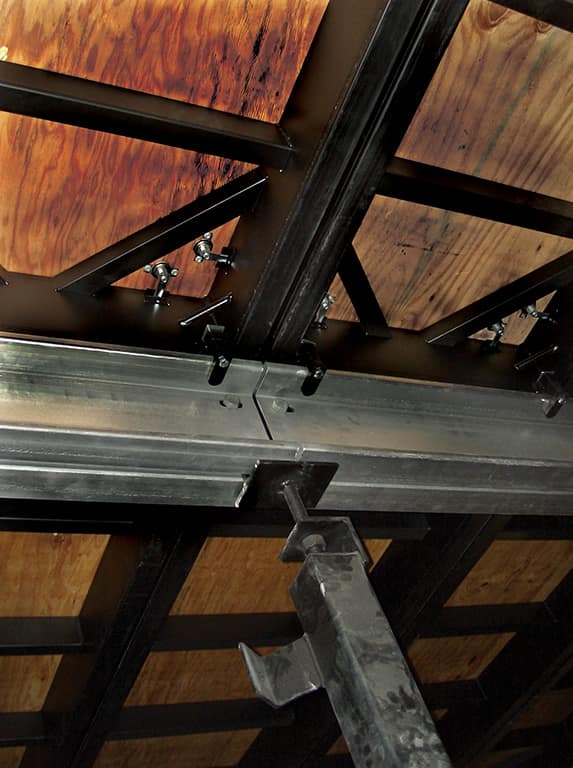
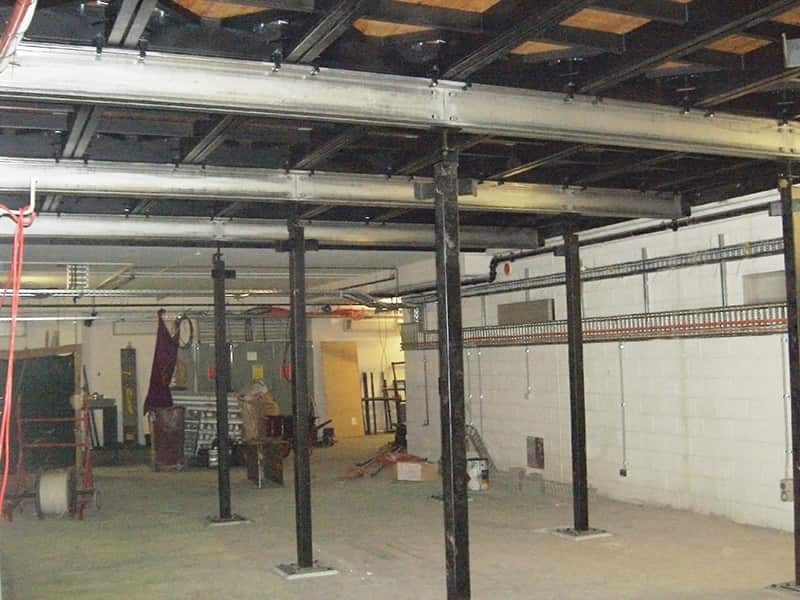
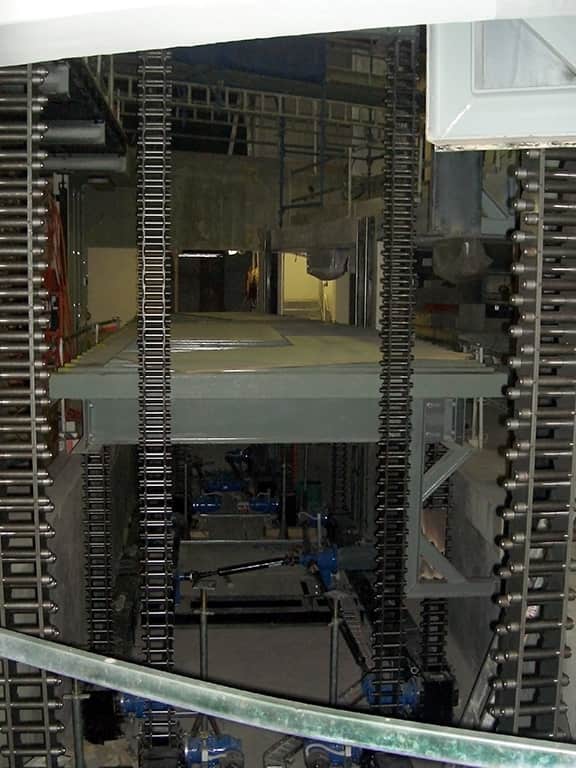
FLEXIBILITY
Because there is no such thing as a standard format for an MTC production, the venue has been designed from the outset to allow almost anything to be done, almost anywhere. While some of the possibilities for production, performance and events could be imagined and, even catered for directly in the plans, it’s clearly impossible to build in adequate facilities for the as-yet-unimagined requirements that will arise during the many decades that the building will be in use.
As the very model of a modern major production house, there are clusters of three-phase power, technical power outlets, data feeds and audio tie-lines secreted in every nook and cranny of the building; from the roof to the staircase landings, and from the workshops to the offices, the ceiling voids, and probably also in the cleaner’s cupboard.
Any place in the building where it is even remotely possible to want to hang anything – from a drape to a Christmas decoration, a length of rope, or couple of lights, to an advertising banner or a circus performer – you’ll find strengthened and rated rigging attachment points. Water, drainage and compressed air lines are run to the roof, all sides and levels of the stage house, everywhere you can imagine backstage, and of course the pit and all over the under-stage area. These are provisions for the unlikely and the unusual, but the nevertheless conceivable.
What happens if you need 200 Amps of 400Hz/110V power in the greenroom or a chilled glycol feed in the control room, a satellite antenna feed in the orchestra pit, a gas flame in the middle of the auditorium or half a dozen HD television camera feeds from the Lawler Studio to an outside broadcast van in the loading dock? How can you achieve these feats without compromising public access paths, fire isolation integrity, or performing serious building works?
The answer chosen by MTC, was to install a series of resealable ‘mouse holes’ in every internal wall, floor and ceiling in the building, enabling any space to be connected to any other space, using nothing more sophisticated than a short step ladder. In the photo you can see that the mouse holes are constructed from standard plumbing pipes and access covers. Fire isolation is maintained through the use of fire-rated bean bags packed with fire-rated pellets of equivalent value to the wall material. Once a cable, hose or pipe has been run through a mouse hole, the bean bags are re-packed into the hole to restore the fire isolation.
STAGE FLOOR
The stage floor of a performing venue is always a bitter bone of contention. Directors frequently want the ability to structure entrances and exits in the vertical as well as the horizontal plane. Stage designers love to explore every skerrick of the stage volume to create the space for the production, by using staircases and putting holes through the floor. Production managers and head carpenters, on the other hand, are always under time and budgetary pressure to have the stage available for fit-up and technical rehearsals. But making good the floor from a previous production, or installing floor traps for the next one, requires areas of the stage to be closed off for safety purposes and engages teams of carpenters and mechanists who could otherwise be involved in turning the venue around.
The solution devised by project manager Craig Gamble for the Sumner Theatre approaches the problem from the opposite direction: there is no permanent stage floor. In the manner of an IT room, the entire stage deck is constructed from easily demountable uniform modules that can be interchanged with pre-built replacement units with the necessary traps already in place. The make-good process simply involves replacing the modified floor module with a standard unit. All preparation and construction takes place off-site, with replacement modules interchanged at the start of the fit-up. While this may seem relatively simple, there were some stringent engineering requirements for ShowTrek during the development of the stage floor system to allow the floor to carry not only the large distributed weights of stage sets, but also the substantial point loads of self-propelled elevated work platforms, like the Sumner’s excellent 2.7-tonne Haulotte Star 10.
The only section of the stage floor that isn’t completely removable is the forestage, which consists of three independent lifts powered by Serapid’s LinkLift actuators. The lifts can be set at substage level to form an orchestra pit, at auditorium floor level to extend the seating capacity of the theatre, or at stage level to become a forestage. As the additional auditorium seating wagons are stored beneath the auditorium in the under-stage area, the lifts also serve to transport these seat units to their auditorium position.
DRAMATIS PERSONAE
Client: Melbourne Theatre Company a department of University of Melbourne
Project partners: State Gov Victoria, Arts Victoria
Architect: Ian McDougall and Peter Bickle of Ashton Raggat McDougall
Project Manager: Major Projects Victoria
Lighting Design (public areas): John Ford of Electrolight
Principal Theatre Consultant: Denis Irving of Entertech
Theatre & Acoustic Consultants: Arup
Theatre Development Manager: Craig Gamble
Services Consultants: Umow Lai
Builder: Bovis Lend Lease
Primary Theatre Engineering Contractor: Jands
Jands subcontractors:
Audio Systems: Rutledge Engineering
Proscenium & Demountable Floor Systems Construction: ShowTrek Productions
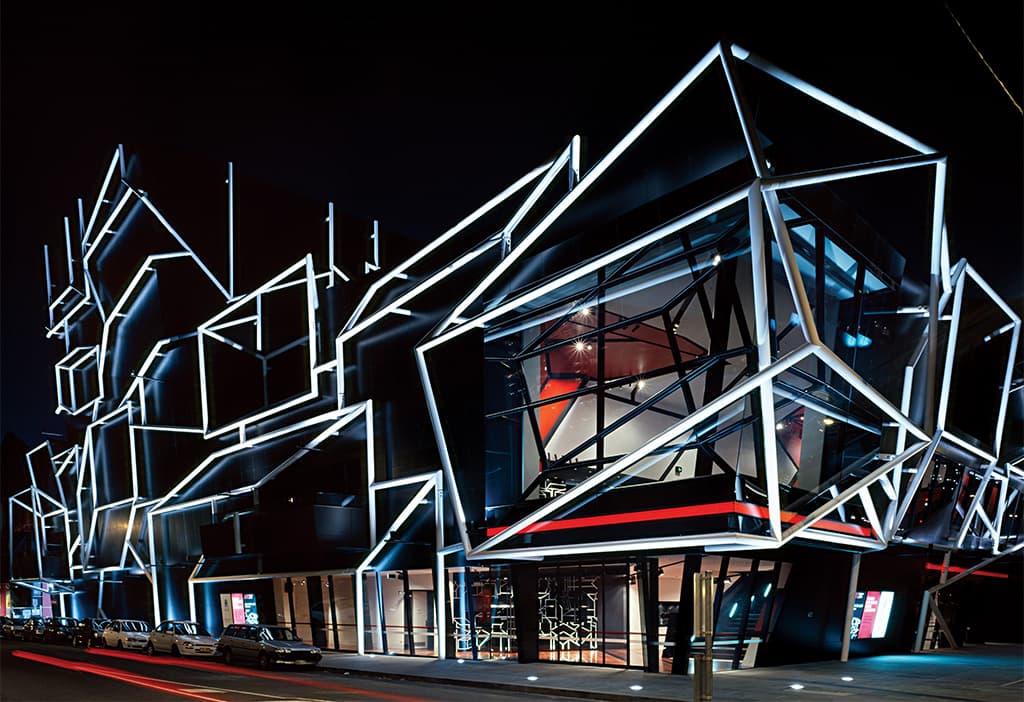
The exterior of the MTC Theatre. The distorted, forced-perspective of the building’s outline resolves into a neat set of boxes when viewed from the footpath near the corner of St Kilda Road and Southbank Boulevard, outside the National Gallery of Victoria.
FOLLOWSPOT BRIDGE
Although only a few of MTC’s productions use followspots, it was essential for the theatre to have followspot positions that provide both a safe working platform for the operators and a good lighting angle. Such a place is the bridge built on the level above the control rooms. In keeping with the brief for maximum flexibility in the venue, any point on the bridge can be used for followspots, special effects equipment, television broadcast or closed circuit video cameras, projection systems, musicians, or even as a performer’s entrance or balcony. Using a system developed by Jands, the entire wall between the bridge and the auditorium can be electrically raised or lowered in independent two-metre sections to create any arrangement of portals or slots in the rear wall. Of course, this bridge is supplied with all of the usual electrical, audio and data services, and is accessible through the mouse hole network and via staircase to the control room.
There is also a series of similarly cabled slots that can be opened as required in the side walls of the auditorium, to provide positions for lighting booms, loudspeakers, alternative followspot positions, effects equipment, projectors, scenery or even performers.
HOUSE LIGHTING
In addition to the conventional Source 4 Pars used for house lighting, the architect proposed to have sections of the walls of the auditorium display quotes from famous productions and playwrights. While the idea was enthusiastically accepted, the proposed display system – an array of addressable colour changing LED pixels spread across the upper parts of the auditorium walls – was fairly swiftly costed out of existence. When MTC were advised that the auditorium wall panelling had to be perforated in order to meet the acoustic requirements of the room, they implemented a traditional theatrical solution to create the so-called Word Walls. In place of a matrix of tens of thousands of LEDs, the words were created by drilling patterns of holes in sheets of 32mm plywood which were then mounted over the required sound deadening voids painted white inside. The void space of each wall panel is illuminated by a Space Cannon Athena RGB LED washlight to form a lightbox. The overall effect is virtually indistinguishable from the original concept and the colours of the words can be changed with ease. The one drawback is that short of replacing the drilled ply sheets, it’s no longer possible to change the wording.
TO INFINITY & BEYOND
Unlike its equally impressive next-door neighbour, the Melbourne Recital Centre [see Issue 4], that was built to host new productions with new requirements every few days, the MTC theatre building was built to house a specific company producing shows with complex requirements, and runs measured in weeks and months rather than days. The type of flexibility that has been incorporated into this carefully thought out building leaves MTC with a clear path forward into the unknowns of future technologies, scripts, designers and directors.
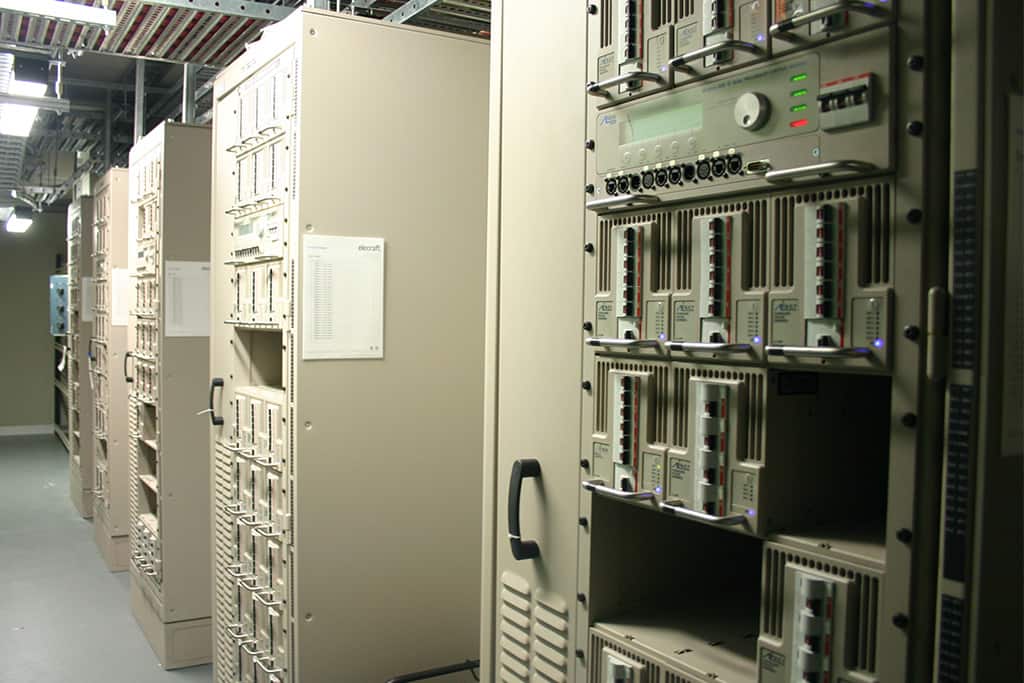
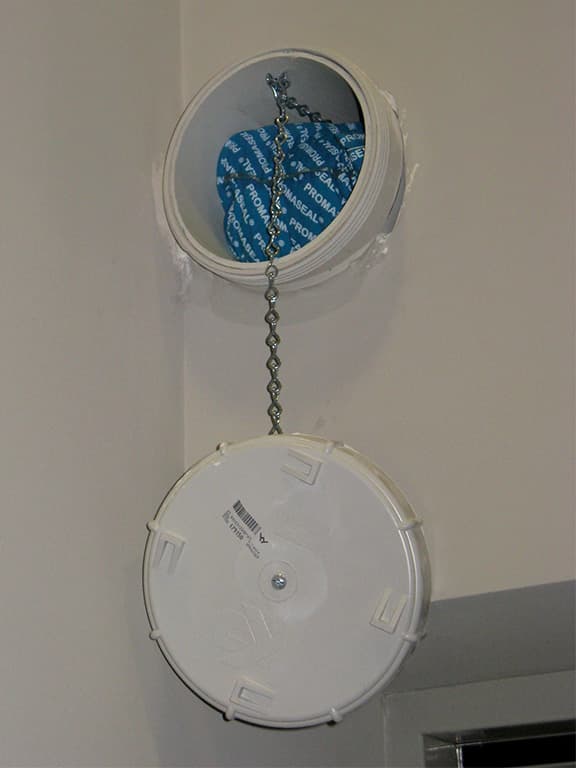
EQUIPMENT LIST
STAGING
Flying System
- Grid weight load limit 30 tonnes
- Controller: Stage Technologies Nomad
- 54 x 500kg power flying lines (Jands SP650 servo hoists) at 200mm centres upstage from the setting line
- 6 x 500kg power flying lines (Jands SP650 servo hoists) at 300mm centres downstage from the setting line
- 4 x 500kg power flying lines (Jands SP650 servo hoists) as panorama bars (2 on each side of stage)
- 6 x 250kg ASM P250 servo high speed band hoists as spot lines
Forestage Lift
- 3 sections on Serapid Linklift actuators
Drapes
- 9 x pairs flat black wool legs 9500(h) x 4000(w)
- 7 x borders flat black wool 5000(h) x 18000(w)
- 2 x pairs flat traveller curtains, black wool 10000(h) x 9500(w) each panel
- 1 x white filled-gauze cyclorama 9500(h) x 30000(w)
- 1 x plastic cyclorama 10000(h) x 17000(w)
- 2 x sharkstooth gauze, black 9500(h) x 17000(w)
- 1 x sharkstooth gauze, grey 9500(h) x 17000(w)
- 1 x smother curtain, flat black wool 9500(h) x 17000(w)
- 4 x Triple -E traveller tracks 18000 in length
- 3 x cyclorama stretcher frames
AUDIO
Console
- Yamaha DM 1000
Speakers
- 7 x Meyer UPJ-1 speakers. Main front of house
- 9 x Meyer UPM-1P speakers Auditorium surround system. Permanently mounted in auditorium walls
- 6 x Meyer MM-4 speakers. Front fill
- 2 x Meyer M1D Sub Bass speakers,
- 4 x Meyer UPJ-1 speakers. Foldback and effects
- 4 x Meyer UPM-1P speakers. Foldback and effects
RESPONSES