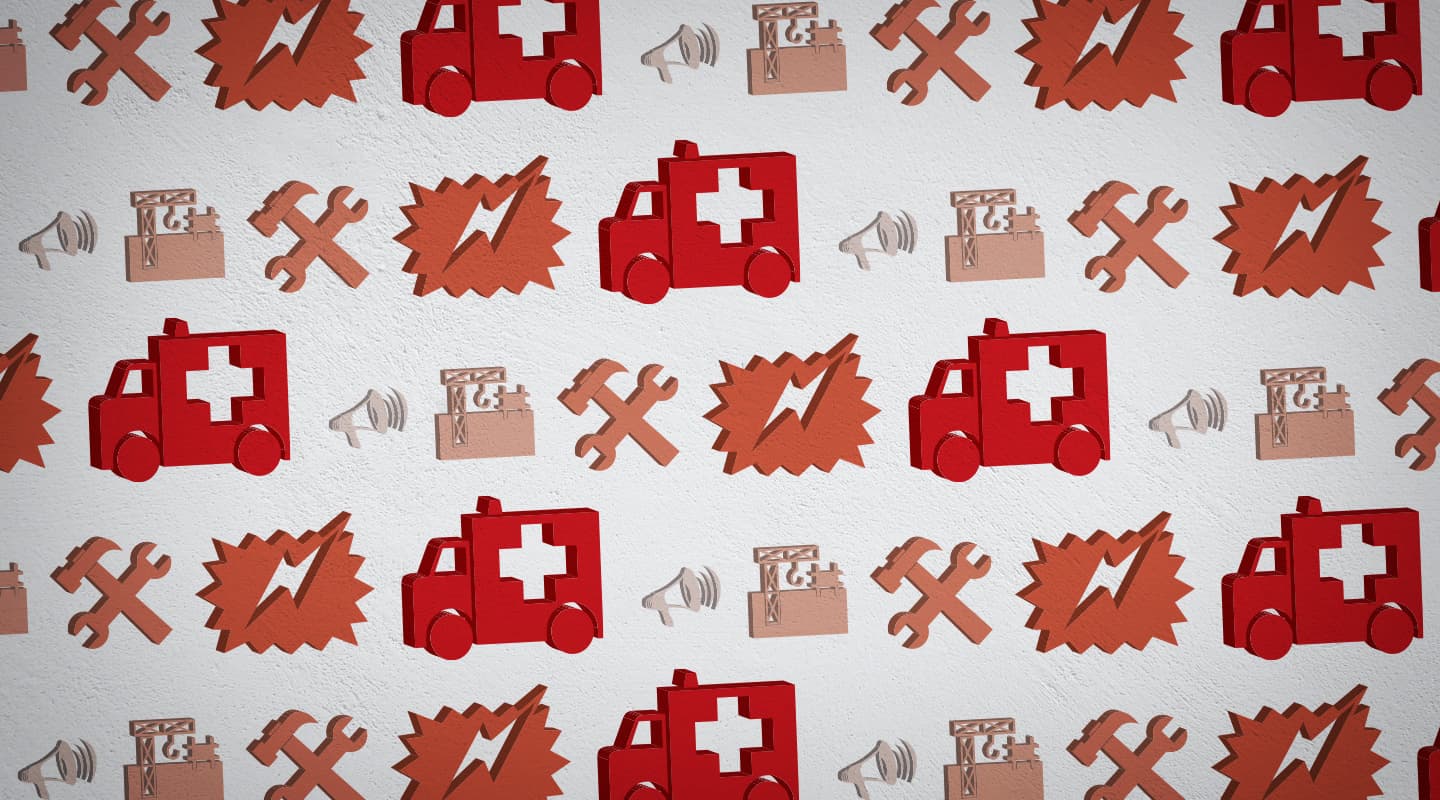
Risky Business
OH&S policies aren’t just the preserve of big departments.
Text:/ Gep Blake
Firstly, an important disclaimer:
The material in this article is of a general nature and is intended to stimulate discussion and further research. It does not constitute specific advice and should not be relied upon to do so. The author, publisher and their agents are not responsible for any actions taken or not taken on the basis of any information included or omitted herein. Appropriately qualified professionals should be consulted.
We all want to get home in one piece at the end of the day and every individual who works in Australia has the right to a safe workplace. Conversely, every worker has an obligation to perform his or her tasks in a way that does not endanger himself, herself or anyone else.
These days, most medium to larger organisations will have reasonably comprehensive Occupational Health & Safety (OHS) policies and procedures with Health & Safety Representatives (HSRs), committees (often even whole departments) to develop and oversee safe methods of work within their appropriate fields, but what about contractors and small business? The audio visual industry employs a great many people on an ad hoc basis according to the needs and budgets of different productions and events, so how can an individual or a very small production company begin to address Occupational Health & Safety?
There are many guidelines, Australian Standards, Safe Work Method Statements (SWMS), Material Safety Data Sheets (MSDS), Ergonomics procedures and so on that are available online – there are some suggested links below. Given the infinite variety of situations you can be confronted with, it’s difficult (if not impossible) to be completely prescriptive. However, there are some basic, underpinning principles that can be used to work out how to approach different activities from an OHS perspective. They can be broken down into three categories – Hazard Identification, Risk Assessment and Risk Control.
HAZARD IDENTIFICATION
This means exactly what it says – identify the hazards! Evaluate the task or activity and try to see or imagine what could go wrong. Look at what is being done and by whom. Do the people who will be carrying out this activity (whether it’s you or someone else) have the appropriate skills and/or qualifications to operate the required machinery? Are they experienced and capable? Are there cables that can be tripped over? There may be fairly obvious hazards, for example, focussing lights on a high gantry could involve working with electricity in a confined space at a significant height. But even apparently simple activities can have inherent and often unseen dangers. Working at a mixing console that has been set up at the wrong height even for short periods can cause neck strain, lower back problems, headaches and more.
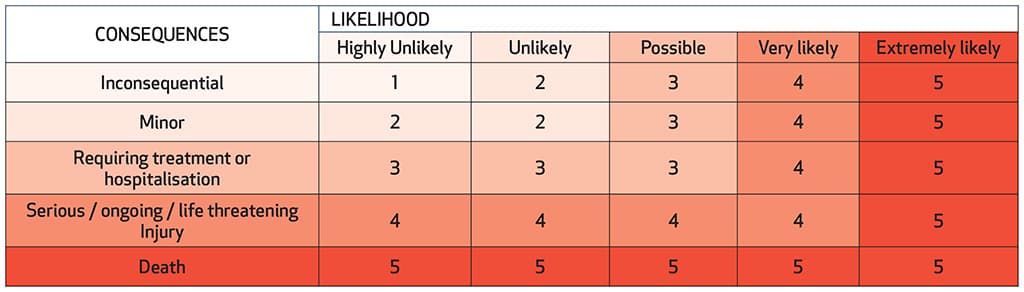
RISK ASSESSMENT
This one isn’t tricky either: assess the likelihood of an incident occurring versus the severity of the possible consequences. This is something you do almost constantly without even realising you’re doing it. Picture yourself standing on the kerb attempting to cross a busy street. You look left – no traffic. You look right and there’s a huge cement truck hurtling towards you about a hundred metres up the road. Now, you might do some subconscious triangulation and higher mathematics, and decide that you’re likely to make it across the road before impact – you have assessed the likelihood of an incident is low. If, however, your subconscious calculations are incorrect or you twist an ankle and you connect with the truck, it’s reasonably certain the consequences will be severe. You may decide on that basis it’s not worth the risk and wait for the truck to pass.
An effective and common tool used to assess risk is a risk matrix. One axis indicates the likelihood of an incident occurring and the other axis indicates the degree of severity of the consequences.
Using a matrix helps you to make a more objective assessment of a given risk, give it a rating and plan accordingly. For example, according to the accompanying chart you may consider it highly unlikely that an automated fader will shut unexpectedly, and if it did, you may consider it inconsequential. This hazard would therefore have a risk rating of 1. You may also be of the opinion that it is highly unlikely that a member of the public will interfere with a poorly insulated three phase power board hidden behind set dressing… but if they do, it would almost certainly result in a death giving that hazard risk a rating of 5.
So, an arbitrary set of actions corresponding to the ratings for the matrix above could be:
- No action required.
- Should be addressed as time and budget permits or within three months (or an appropriate time span).
- Requires immediate attention – Supervise the activity and control the immediate risk, any ongoing risk must be resolved within two weeks.
- Requires immediate attention – Supervise the activity and control the immediate risk, any ongoing risk must be resolved within 24 hours.
- Requires immediate attention – Do not proceed with this activity until risk is eliminated.
“”
even apparently simple activities can have inherent and often unseen dangers
RISK MINIMISATION: THE HIERARCHY OF CONTROLS
So then, how do we go about controlling or minimising the risks that have been identified? The methods used to minimise risks are generally ordered into a hierarchy of six controls.
Elimination: The best control from an OHS perspective is to eliminate the risk altogether. Simply do not carry out the task or operate the equipment in question. This must be weighed up against the importance of the overall project and what impact the elimination of one aspect will have. For example, a client may wish to have pyrotechnics at an event but as the producer you may decide that the hay bale dance at the 100-year-old shearing shed full of lanoline-soaked timber in the middle of summer is not really a safe environment to allow.
Substitution: Substitute a safer piece of equipment or procedure for the one that’s deemed to pose an unacceptable risk. Perhaps an impressive show using cooler LED lights might do the trick rather than fire and explosions.
Isolation: Isolate the risky equipment or procedure. Put up fences, barricades etc to prevent access by unauthorised or unqualified individuals.
Engineering Controls: Use safety guards, shields or other mechanical aids to lessen the chance of an incident.
Administrative Controls: Warning signs, regulations, Safe Work Method Statements are all examples of administrative controls.
PERSONAL PROTECTIVE EQUIPMENT (PPE)
It is often assumed that the use of PPE is the be all and end all of safety. In fact, it’s actually the ‘last line of defence’. Safety goggles, helmets, gloves, earmuffs and so on are the least effective risk controls. Where appropriate, PPE should certainly be used but never relied upon as the only risk control.
The one general rule of thumb is: If you’re not absolutely confident that the task at hand has an acceptable level of risk, don’t do it.
LIFETIME GUARANTEE
Managing Occupational Health & Safety can feel overwhelming. Whether part of an established larger organisation or operating as a sole contractor, the AV professional is often faced with myriad difficult and potentially dangerous situations – anything from working at heights to pyrotechnics. Sometimes state and federal regulations and guidelines appear to differ and the penalties for breaching legislation can be severe. There are mighty big fines, or, in the case of wilful negligence, individuals can find themselves doing time with Patsy Cline.
But when you’re thinking it’s too expensive to replace the old scissorlift; or you don’t have time to make sure your mains power cables are all tested and tagged; or it’s too inconvenient to wear the approved safety harness – don’t worry about the fines or the jail terms… just think about how you’d feel sitting in a courtroom trying to explain to a family that their wife/brother/father isn’t around anymore because you found things inconvenient.
RESPONSES